|
Mobile: 07777 697723 Office:
01992 464131
Email: Andrew1Hooper@btinternet.com
Flat Roof Replacement |
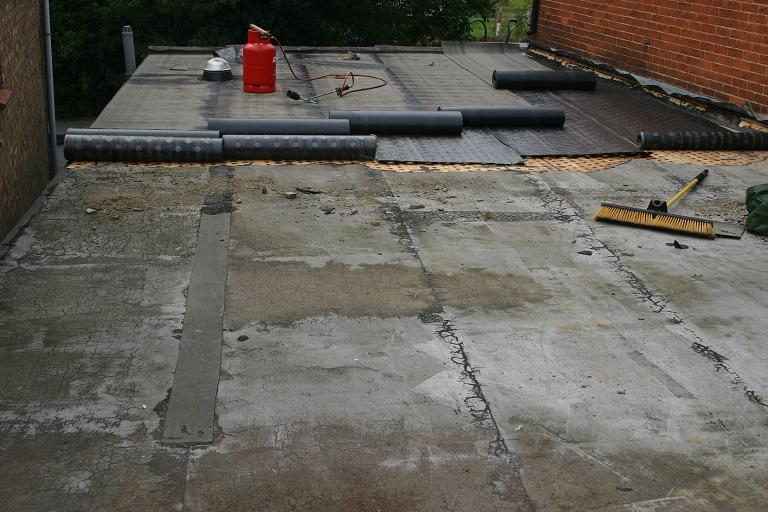
|
Tollesbury, Essex |
Please see illustrated a few of the Thousands of flat roofs we have replaced and renewed
over our 30 years as a roofing company repairing and renewing all types of roof. One of the most important qualities
to installing a first class roof to our customers is our experience in the roofing industry. Offering all aspects of
roofing from stuctural to aestetic look gives our customers peice of mind that when there roof has been renewed by us it will
not only stand the test of time but will also be pleasing to look at as importantly as any aspect of a sound roof is importance
to detail. All our flat roof renewals have life ecxpectency of between 25-35years and roof renewals that we completed
over 30 years ago are still standing the test of time and giving our customers great value for money.
Flat Roof Replacement |
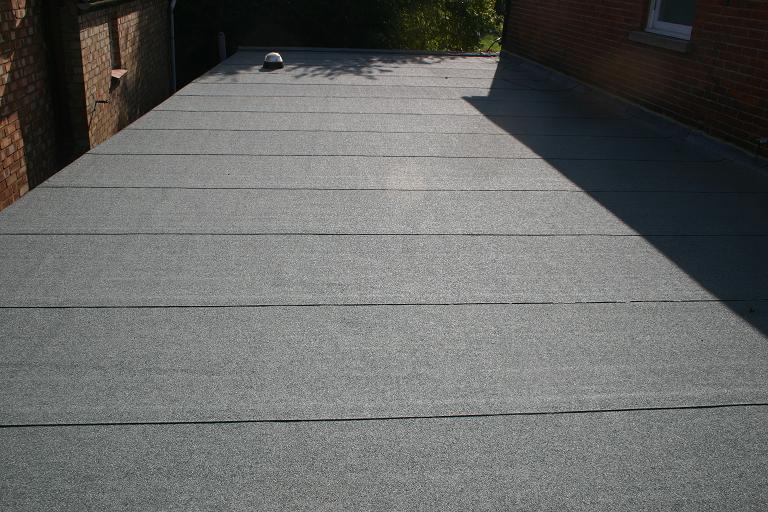
|
Tollesbury, Essex |
Above and on the left is a flat roof renewal in Tollesbury Essex, this flat roof repair was in 2007 on a domestic/commercial
property. All roof coverings were stripped and cleared from site, new torch on roof covering was installed with a sun tube
fitted for a shower room
Fire Damaged Flat Roof Replacement |
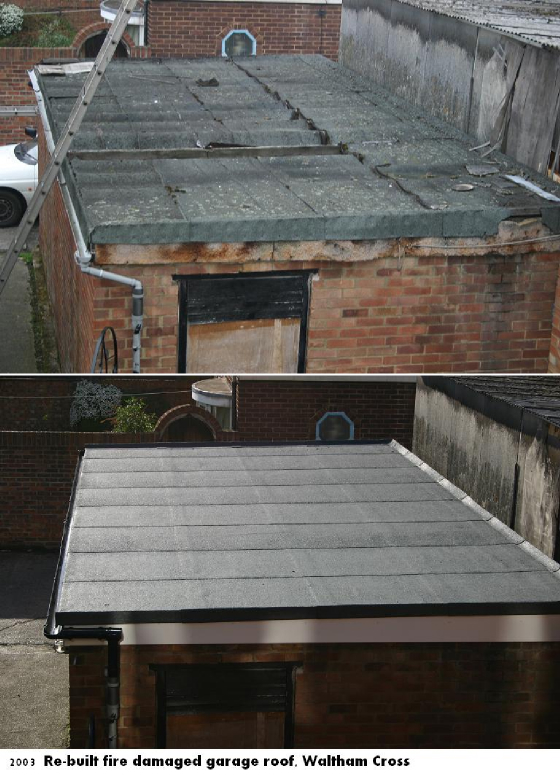
|
Waltham Cross, Essex |
Flat Roof Replacement |
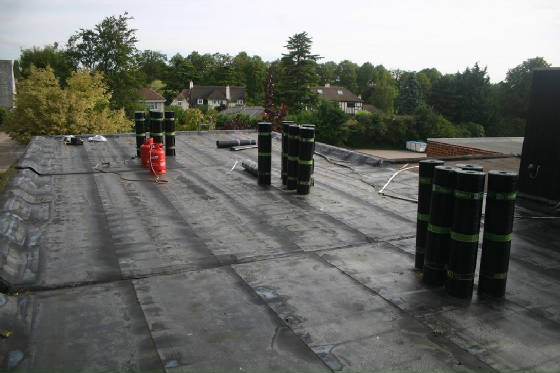
|
Broxbourne Sports Club |
Chorleywood |
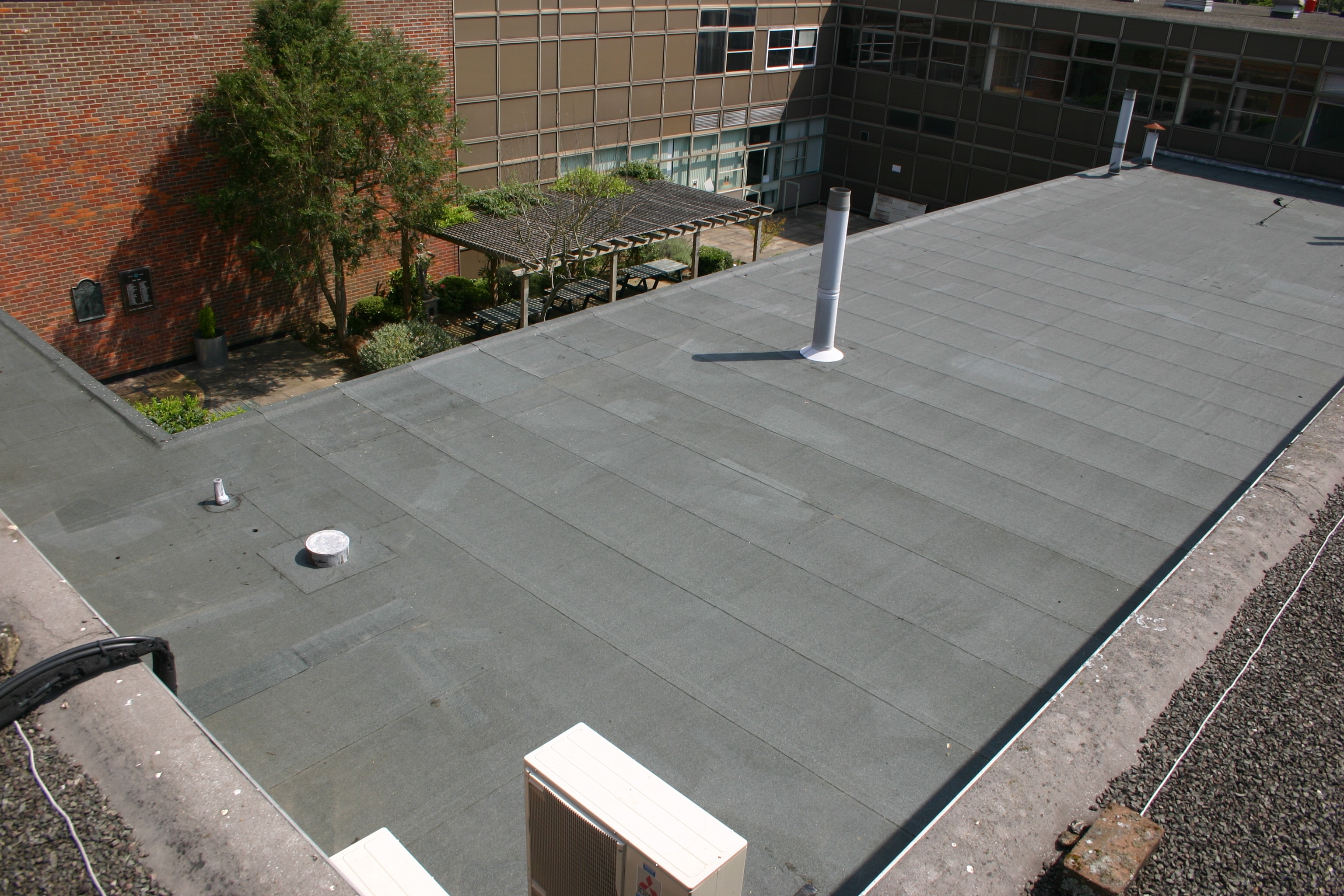
|
St.Clement Danes School |
Broxbourne Sports Club Flat Roof
Renewal above Squash Courts, all our roof works are carried out to the highest standard to get the longest possible
life span from a flat roof, materials use when renewing a flat roof are of the highest standard so you can be assured
of a roof system that will deliver you the longest roof life span that a flat roofing system can deliver in the
roofing industry. On
the left is a new flat roof re-build after fire damage in Enfield London, The roof required a complete re-build with new timber
Joists and ply decking, all fascias, soffits and Gutters were renewed in pvc
undefined |
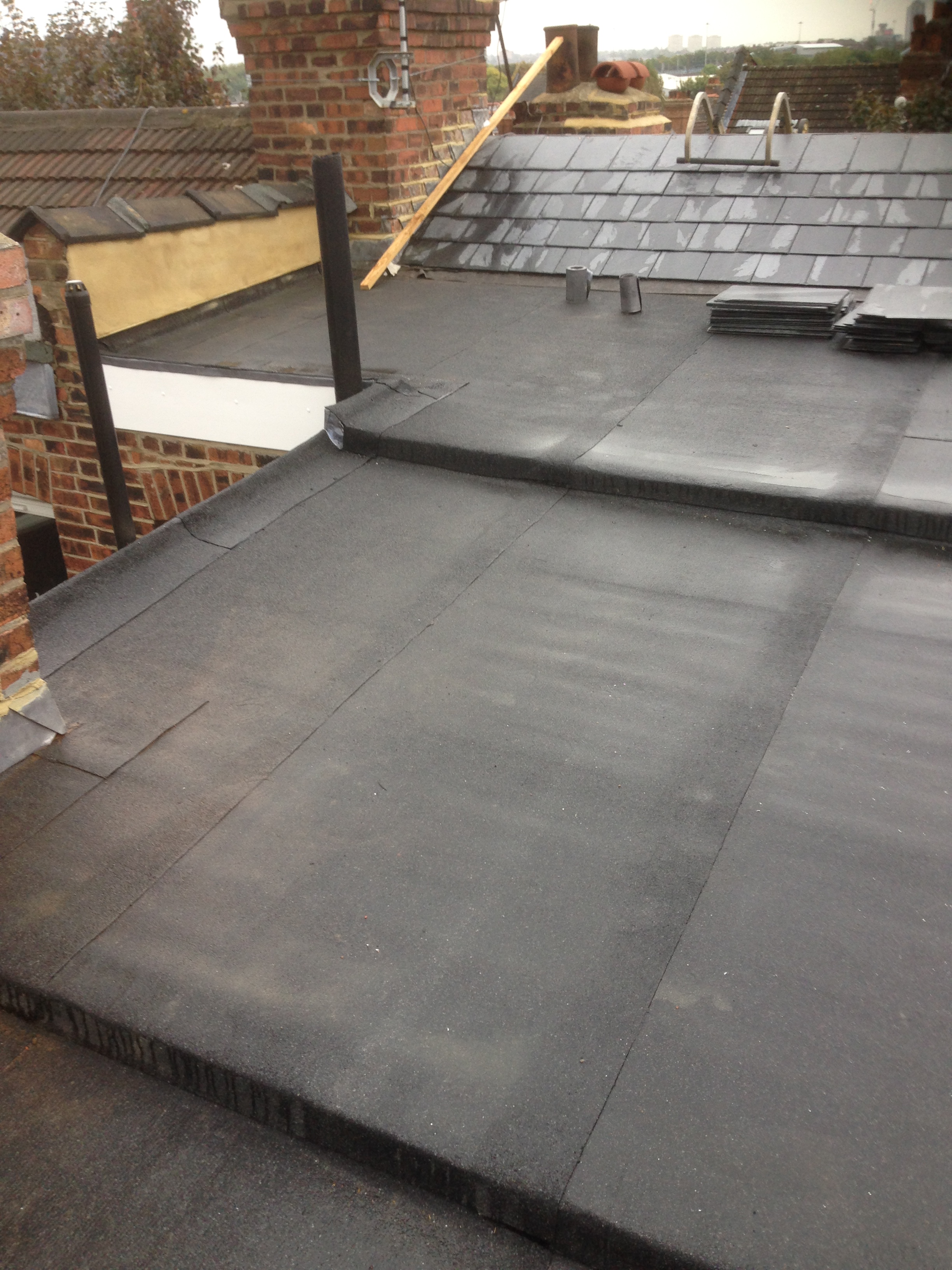
|
undefined |
Flat Roofing Repair |
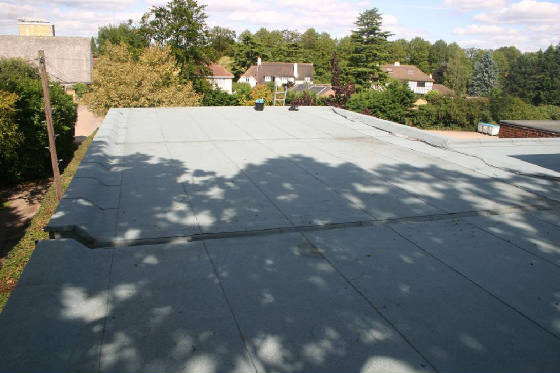
|
Broxbourne Sports Club Flat roof repair |
Above is Broxbourne Sports club for Tennis/Cricket/Squash and Football, we renewed the
Squash club roof with Heat bonded torch on felt
Flat Roof Repairs |
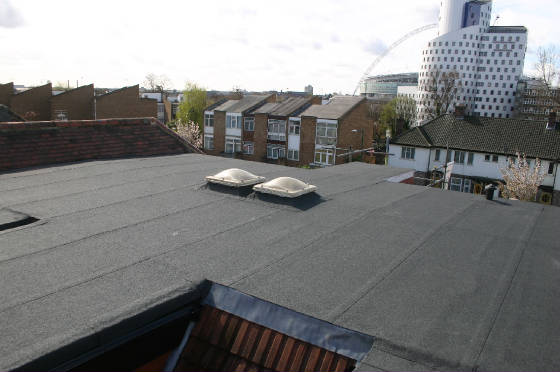
|
Flat roof repairs & Replacement |
On the left is a new flat roof on a loft conversion in London, All old roof coverings were
removed, lowered and cleared from site and a new torch on felt roof system installed
Flat Roof Repairs |
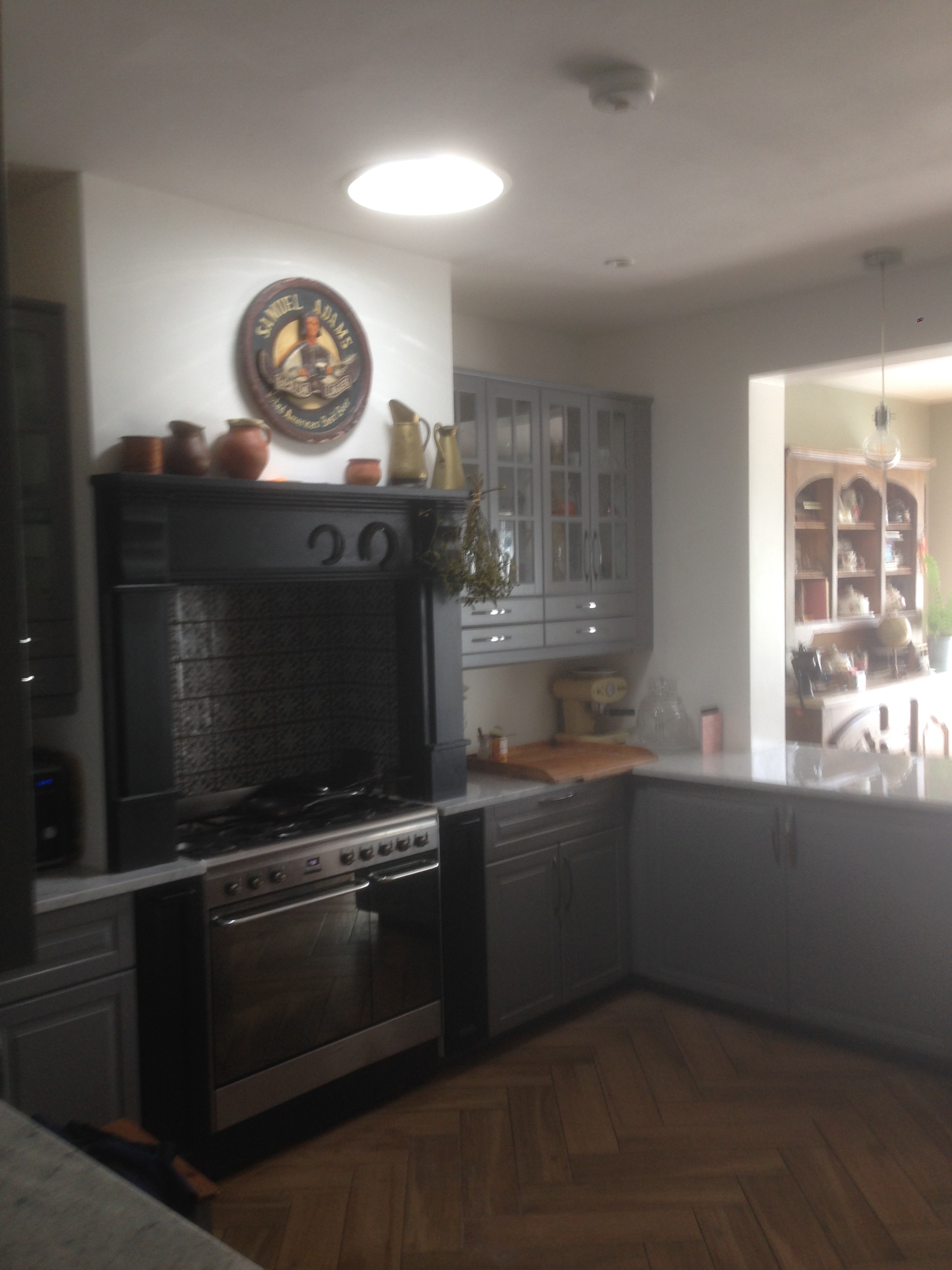
|
Flat roof repairs & Replacement |
Above is a Flat Roof service we carried out in maida vale west London, the
roofing felt and decking were stripped, 18mm Ply roof decking fitted with the 3 layer felt roofing system installed.
New Lead flashings were fitted to all parapit walls.
Home Page
Please Click for Contact Details
We are a local company established since the early 80s with a high level
of experience in the flat roofing industry. The main bulk of our flat roofing services are domestic home flat roofing
which will involve every aspect of flat roof work. If you require a Free quote for the renewal and replacement of your
flat roof or advice on the best flat roofing options please feel free to contact me Andy Hooper on the above number.
The flat roof is is often thought to be the worst of all roof constructions,
mainly due to its shorter life span a flat roof has against the pitched roof, it is often said that flat roofing is
nothing but trouble but this is not true as most flat roofs correctly installed by a roofing contractor with a long experience
in flat roofing and other aspects of roofing will last between 25 to 30 years and beyond if left alone with
nobody constantly walking on them without care. The other and main reason that flat roofs can be a problem is that the
roof was poorly installed by people roofing of little experience or pride of there roofing work. This lack of pride
in there roofing is easy to spot as they speed away with your hard earned cash because cash is often there 1st requirement
leaving you little room for complaint when the roof starts leaking. As you can see from the website the new flat
roofing in the pictures are as all our flat roofing installations completed to the manufactures specifications and all the
flat roofing materials are of a high standard which will provide a flat roof that will stand the test of time
and give our customers peace of mind and value for money as our exaust nears the corner and beyond. If you would
like a FREE QUOTE for the renewal of a flat roof please call one of the above number or e-mail your details and we will get
back to you.
. .
Flat roof Flat roofs in Israel  Flat roof in Los Angeles  Flat roof in Warszawa Centralna railway station in Poland (1975) A flat roof is a roof which is almost level in contrast to the many types
of sloped roofs. The slope of a roof is properly known as its pitch and flat roofs have up to approximately 10°.[1] Flat roofs are an ancient form mostly used in arid climates and allow the roof space to be used as a living space or a living roof. Flat roofs, or "low-slope" roofs, are also commonly found on commercial buildings throughout the world. The National Roofing Contractors Association defines a low-slope roof as having a slope of 3 in 12 (1:4) or less.[2] Flat roofs exist all over the world, and each area has its own tradition or preference for materials used. In
warmer climates, where there is less rainfall and freezing is unlikely to occur, many flat roofs are simply built of masonry
or concrete and this is good at keeping out the heat of the sun and cheap and easy to build where timber is not readily available.
In areas where the roof could become saturated by rain and leak, or where water soaked into the brickwork could freeze to
ice and thus lead to 'blowing' (breaking up of the mortar/brickwork/concrete by the expansion of ice as it forms)
these roofs are not suitable. Flat roofs are characteristic of the Egyptian, Persian, and Arabian styles of architecture.[3] Around the world, many modern commercial buildings have flat roofs. The roofs are usually clad with a deeper profile roof sheet (usually 40mm deep or greater). This gives
the roof sheet very high water carrying capacity and allows the roof sheets to be more than 60 metres long in some cases.
The pitch of this type of roof is usually between 1 and 3 degrees depending upon sheet length. Construction methods[edit]Any sheet of material used to cover a flat or low-pitched roof is usually known as a membrane
and the primary purpose of these membranes is to waterproof the roof area. Materials that cover flat roofs typically allow
the water to run off from a slight inclination or camber into a gutter system. Water from some flat roofs such as on garden sheds
sometimes flows freely off the edge of a roof, though gutter systems are of advantage in keeping both walls and foundations
dry. Gutters on smaller roofs often lead water directly onto the ground, or better, into a specially made soakaway. Gutters
on larger roofs usually lead water into the rainwater drainage system of any built up area. Occasionally, however, flat roofs
are designed to collect water in a pool, usually for aesthetic purposes, or for rainwater buffering. Traditionally most
flat roofs in the western world make use of tar or asphalt more usually felt paper applied over roof decking to keep a building watertight. The felt paper is in turn
covered with a flood coat of bitumen (asphalt or tar) and then gravel to keep the sun's heat, ultraviolet light and weather off it and helps protect it from cracking or blistering and
degradation. Roof decking is usually of plywood, chipboard or oriented strand board (OSB, also known as Sterling board) of around 18 mm thickness, steel or concrete. The mopping of bitumen is applied
in two or more coats (usually three or four) as a hot liquid, heated in a kettle. A flooded coat of bitumen is applied over
the felts and gravel is embedded in the hot bitumen. A main reason for failure of these traditional roofs is ignorance
or lack of maintenance where people or events cause the gravel to be moved or removed from the roof membrane, commonly called
a built-up roof, thus exposing it to weather and sun. Cracking and blistering occurs and eventually water gets in. Roofing
felts are usually a 'paper' or fiber material impregnated in bitumen. As gravel cannot protect tarpaper surfaces where
they rise vertically from the roof such as on parapet walls or upstands, the felts are usually coated with bitumen and protected
by sheet metal flashings called gravel stops. The gravel stop terminates the roofing, preventing water from running underneath
the roofing and preventing the gravel surfacing from washing off in heavy rains. In some microclimates or shaded areas
felt roofs can last well in relation to the cost of materials purchase and cost of laying them. The cost of membranes such
as EPDM rubber has come down over recent years[when?]. If a leak does occur on a flat roof, damage often goes unnoticed for considerable time as water penetrates
and soaks the decking and any insulation and/or structure beneath. This can lead to expensive damage from the rot which often
develops and if left can weaken the roof structure. There are health risks to people and animals breathing the mould spores:
the severity of this health risk remains a debated point. While the insulation is wet, the "R" value is essentially
destroyed. If dealing with an organic insulation, the most common solution is removing and replacing the damaged area. If
the problem is detected early enough, the insulation may be saved by repairing the leak, but if it has progressed to creating
a sunken area, it may be too late. One problem with maintaining flat roofs is that if water does penetrate the barrier
covering, it can travel a long way before causing visible damage or leaking into a building where it can be seen. Thus, it
is not easy to find the source of the leak in order to repair it. Once underlying roof decking is soaked, it often sags, creating
more room for water to accumulate and further worsening the problem. Another common reason for failure of flat roofs
is lack of drain maintenance where gravel, leaves and debris block water outlets (be they spigots, drains, downpipes or gutters).
This causes a pressure head of water (the deeper the water, the greater the pressure) which can force more water into the
smallest hole or crack. In colder climates, puddling water can freeze, breaking up the roof surface as the ice expands. It
is therefore important to maintain your flat roof to avoid excessive repair. An important consideration in tarred flat
roof quality is knowing that the common term 'tar' applies to rather different products: tar or pitch (which is derived
from wood resins), coal tar, asphalt and bitumen. Some of these products appear to have been interchanged in their use and
are sometimes used inappropriately, as each has different characteristics, for example whether or not the product can soak
into wood, its anti-fungal properties and its reaction to exposure to sun, weather, and varying temperatures. Modern
flat roofs can use single large factory-made sheets such as EPDM synthetic rubber, polyvinyl chloride (PVC), thermoplastic polyolefin (TPO) etc. Although usually of excellent quality, one-piece membranes are called single plies are used today on many
large commercial buildings. Modified bitumen membranes which are widely available in one-metre widths are bonded together
in either hot or cold seaming processes during the fitting process, where labour skill and training play a large part in determining
the quality of roof protection attained. Reasons for not using one-piece membranes include practicality and cost: on all but
the smallest of roofs it can be difficult to lift a huge and heavy membrane (a crane or lift is required) and if there is
any wind at all it can be difficult to control and bond the membrane smoothly and properly to the roof. Detailing of
these systems also plays a part in success or failure: In some systems ready-made details (such as internal and external corners,
through-roof pipe flashings, cable or skylight flashings etc.) are available from the membrane manufacturer and can be well
bonded to the main sheet, whereas with materials such as tar papers this is usually not the case - a fitter has to construct
these shapes on-site. Success depends largely on their levels of skill, enthusiasm and training - results can vary hugely. Metals
are also used for flat roofs: lead (welded or folded-seamed), tin (folded, soldered or folded-seamed) or copper. These are
often expensive options and vulnerable to being stolen and sold as scrap metal. Flat roofs tend to be sensitive to human
traffic. Anything which produces a crack or puncture in the waterproofing membrane can quite readily lead to leaks. Flat roofs
can fail, for example; when subsequent work is carried out on the roof, when new through-roof service pipes/cables are installed
or when plant such as air conditioning units are installed. A good roofer should be called to make sure the roof is left properly
watertight before it is left. In trafficked areas, proper advisory/warning signs should be put up and walkways of rubber matting,
wooden or plastic duck-boarding etc. should be installed to protect the roof membrane. On some membranes, even stone or concrete
paving can be fitted. For one-off works, old carpet or smooth wooden planks for workers to walk or stand on will usually provide
reasonable protection. Modernist architecture often viewed the flat roof as a living area. Le Corbusier's theoretical works, particularly Vers une Architecture, and the influential Villa Savoye and Unité d'Habitation prominently feature rooftop terraces. That said, Villa Savoye's roof began leaking almost immediately after the Savoye family moved in. Le Corbusier only
narrowly avoided a lawsuit from the family because they had to flee the country as France succumbed to the German Army in
the Second World War. Flat roof developments[edit]Protected membrane roof[edit]A protected membrane roof (PMR) is a roof where thermal insulation or another material is located above the waterproofing
membrane. Modern green roofs are a type of protected membrane roof. This development has been made possible by the creation
of waterproofing membrane materials that are tolerant of supporting a load and the creation of thermal insulation that is
not easily damaged by water. Frequently, rigid panels made of extruded polystyrene are used in PMR construction. The chief benefit of PMR design is that the covering protects the waterproofing membrane
from thermal shock, ultraviolet light and mechanical damage.[4] One potential disadvantage of protected membrane roof construction is the need for structural strength to support
the weight of ballast that prevents wind from moving rigid foam panels or the weight of plants and growth media for a green
roof. However, when flat roofs are constructed in temperate climates, the need to support snow load makes additional structural strength a common consideration in any event. Protected membrane roofs are sometimes
referred to in the roofing industry as "IRMA" roofs, for "inverted roof membrane assembly". "IRMA"
as a roofing term is a genericized trademark. Originally, "IRMA" was a registered trademark of the Dow Chemical Company and stood for "Insulated Roof Membrane Assembly" and referred to PMRs assembled using Dow brand extruded polystyrene
insulation.[5] Green roofs[edit] Green roof at Prince George's Community College in Largo, MarylandGrass or turf roofs have been around since the Viking times if not far earlier and make for a decorative and durable roof
covering. Green roofs have been made by depositing topsoil or other growth media on flat roofs and seeding them (or allowing them to self-seed
as nature takes its course). Maintenance in the form of simple visible inspection and removal of larger rooting plants allows
these roofs to be successful in that they provide an excellent covering and UV light barrier for the roof waterproofing membrane.
With some systems, the manufacturer requires that a root barrier membrane be laid above the waterproofing membrane. If well
planned and fitted, the mass of the soil or growth medium can provide a good heat buffer for the building - storing the
heat of the sun and releasing it into the building at night and thus keeping inside temperatures more even. Sudden cold spells
are also buffered from the building. One predicted problem with large green roofs is that fire may be able to spread
rapidly across areas of dry grasses and plants when they are dried, for instance, in summer by hot weather: Various countries
stipulate fire barrier areas made of, for example, wide strips of (partly decorative) gravel. Sedum is emerging as a favourite as it is easily transported and requires little maintenance as it is a succulent plant which
remains close to the ground throughout its growth, has mild roots which do not damage the waterproofing membrane and changes
colour in the seasons in greens, browns and purples to give a pleasing effect to the eye. Green-roof water buffering[edit]Water run-off and flash floods have become a problem especially in areas where there is a large amount of paving
such as in inner cities: When rain falls (instead of draining into the ground over a large area as previously) a rainwater
system's pipes take water run-off from huge areas of paving, road surfaces and roof areas - as areas become more
and more built up these systems cope less and less well until even a rain-shower can produce backing up of water from pipes
which cannot remove the large water volume and flooding occurs. By buffering rainfall, such as by fitting green roofs, floods
can be reduced or avoided: the rain is absorbed into the soil/roof medium and runs off the roof bit by bit as the roof becomes
soaked. Roof decks[edit]A modern (since the 1960s) development in the construction of decks, including flat-roof decks, especially when used
as living area or the roof of a commercial structure, is to build a composite steel deck.[6] Types of flat roof coverings[edit] Flat roof of Verisure headquarters at Versoix. Asphalt[edit]Asphalt is an aliphatic compound and in almost all cases a byproduct of the oil industry. Some asphalt is manufactured from oil as the intended purpose,
and this is limited to high-quality asphalt produced for longer lasting asphalt built-up roofs (BUR). Asphalt ages through
photo-oxidation accelerated by heat. As it ages, the asphalts melt point rises and there is a loss of plasticizers. As mass
is lost, the asphalt shrinks and forms a surface similar to alligator skin. Asphalt breaks down slowly in water, and the more
exposure the more rapid the degradation. Asphalt also dissolves readily when exposed to oils and some solvents. There
are four types of roofing asphalt. Each type is created by heating and blowing with oxygen. The longer the process the higher
the melt-point of the asphalt. Therefore, Type I asphalt has characteristics closest to coal tar and can only be used on dead
level surfaces. Type II, is considered flat and can be applied to surfaces up to 1⁄4-in-12 (1:48) slopes. Type
III, is considered to be "steep" asphalt but is limited to slopes up to 2 in 12 (1:6), and Type IV is "special
steep". The drawback is, the longer it is processed, the shorter the life. Dead-level roofs where Type I asphalt is used
as the flood and gravel adhesive perform nearly as well as coal tar. Asphalt roofs are also sustainable by restoring the life
cycle by making repairs and recoating with compatible products. The process can be repeated as necessary at a significant
cost savings with very little impact on the environment. Asphalt BUR is made up of multiple layers of reinforcing plies
and asphalt forming a redundancy of waterproofing layers. The reflectivity of built up roofs depends on the surfacing material
used. Gravel is the most common and they are referred to as asphalt and gravel roofs. Asphalt degradation is a growing concern.
UV-rays oxidize the surface of the asphalt and produce a chalk-like residue. As plasticizers leach out of the asphalt, asphalt
built-up roofs become brittle. Cracking and alligatoring inevitably follows, allowing water to penetrate the system causing
blisters, cracks and leaks. Compared to other systems, installation of asphalt roofs is energy-intensive (hot processes typically
use LP gas as the heat source), and contributes to atmospheric air pollution (toxic, and green-house gases are lost from the
asphalt during installation).  EPDM rubber roof Ethylene propylene diene monomer rubber (EPDM) is a synthetic rubber most commonly used in single-ply roofing because it is readily available and simple to apply. Seaming and detailing
has evolved over the years and is fast, simple and reliable with many membranes including factory applied tape, resulting
in a faster installation. The addition of these tapes has reduced labour by as much as 75%. It is a low-cost membrane,
but when properly applied in appropriate places, its warranted life-span has reached 30 years and its expected lifespan has
reached 50 years. There are three installation methods: ballasted, mechanically attached, and fully adhered. Ballasted
roofs are held in place by large round stones or slabs. Mechanically attached roof membranes are held in place with nails
and are suitable in some applications where wind velocities are not usually high. A drawback is that the nails penetrate the
waterproof membrane; if correctly fastened the membrane is "self-gasketing" and will not leak. Fully adhered installation
methods give the longest performance of the three methods. The most advanced EPDM is combined with a polyester fleece
backing and fabricated with a patented hot-melt adhesive technology which provides consistent bond strength between the fleece backing and the membrane. This results in largely
eliminating shrinkage of the product, whilst still allowing it to stretch up to 300% and move with the building through the
seasons. The fleece improves puncture and tear resistance considerably; 1.1-millimetre (45-mil) EPDM with a fleece backing
is 180% stronger than 1.5-millimetre (60-mil) bare EPDM. Fleece-backed EPDM has a tear strength of 39.9 kN/m (228 lbf/in)
compared to 13.1 kN/m (75 lbf/in) of that without the fleece reinforcement, more than 3 times the strength of non-reinforced
membranes. This thermoset polymer is known for long-term weathering ability and can withstand fluctuations in temperature
and ultraviolet rays. They can also be great energy savers. CPE and CSPE[edit]Chlorosulfonated polyethylene (CSPE) and chlorinated polyethylene (CPE) are nonvulcanized synthetic rubber roofing materials that were used for roofing materials from 1964 until their
almost complete removal/disappearance from the market in 2011. It is more popularly known and referred to as Hypalon. The
product is usually reinforced, and depending upon manufacturer, seams can be heat welded (when both membranes were brand new)
or adhered with a solvent-based adhesive. Over time, however, the materials cure and gain properties similar to most thermoset
materials such as neoprene or EPDM. After environmental concerns in the late 1990's companies began to feel pressured regarding some of the
common adhesives and bonding chemicals, and some jurisdictions passed regulations limiting the use of CSPE membranes. this
caused many manufacturers to scramble to create new ways to manufacture the roofing materials, raising costs as well as concerns
regarding longevity. In June 2009, DuPont, the manufacturer of Hypalon, discontinued the product, followed within a couple
years by nearly every major manufacturer. As a result, CSPE and CPE are no longer available in the US as a full roof membrane,
and repair materials are extremely rare or expensive compared to other membranes.[7] Modified bitumen[edit]Modified bitumen membranes are hybrid roof systems that combine the high technology formulation and prefabrication
benefits of single-ply with the traditional roofing installation techniques used in built-up roofing. The membranes consist
of factory-fabricated layers of asphalt, modified using a plastic or rubber ingredient and combined with a reinforcement.[8] The final modified bitumen sheet goods are typically installed by heating the underside of the roll with a torch,
presenting a significant fire hazard. For this reason, the technique was outlawed in some municipalities when buildings caught
fire, some burning to the ground. This problem was alleviated by strict specifications requiring installation training and
certification as well as on-site supervision. Another problem developed when a lack of standards allowed a manufacturer to
produce the product with insufficient APP, requisite to enhancing the system aging characteristics. A bitumen is a term applied to both coal tar pitch and asphalt products. Modified bitumens were developed in Europe in the 1970s
when Europeans became concerned with the lower performance standards of roofing asphalt. Modifiers were added to replace the
plasticizers that had been removed by advanced methods in the distillation process. The two most common modifiers are atactic polypropylene (APP) from Italy and styrene-butadiene-styrene (SBS) from France. The United States started developing modified bitumen compounds in the late 1970s and early 1980s. APP
was added to asphalt to enhance aging characteristics and was applied to polyester, fiberglass, or polyester and fiberglass
membranes to form a sheet good, cut in manageable lengths for handling. SBS is used as a modifier for enhancing substandard
asphalt and provides a degree of flexibility much like rubber. It also is applied to a myriad of carriers and produced as
a sheet-good in rolls that can be easily handled. Styrene ethylene butadiene styrene (SEBS) is a formulation increasing flexibility of the sheet and longevity. Styrene-isoprene-styrene (SIS) is another modifier used commercially. SIS-modified bitumen is rarely used, is used primarily in self-adhering
sheets, and has very small market share. Cold-applied liquid membranes[edit]A choice for new roofs and roof refurbishment. This type of a roof membrane is generally referred to as liquid roofing and involves the application of a cold liquid roof coating. No open flames or other heat sources (as are required with torch on felts) are needed and the glass fiber reinforced systems
provide seamless waterproofing around roof protrusions and details. Systems are based on flexible thermoset resin systems
such as polyester and polyurethane, and poly(methyl methacrylate) (PMMA). It is important that the membrane is not applied too thin like a paint otherwise failure will result. In
the United Kingdom, liquid coatings are the fastest growing sector of the flat roof refurbishment market. Between 2005 and
2009 the UK's leading manufacturers reported a 70% increase in the roof area covered by the coating systems supplied.[9] Cold-applied liquid rubber offers similar benefits to thermoset resin systems with the added benefit of being
quick to apply and having high elasticity. Although it is comparatively new to the UK market it has been used successfully
in the US market for 20 years. However, EPDM is not an easy substrate to adhere to as is any polyolefin so applying liquid
membranes over EPDM is not easy. When applying a liquid membrane it is possible to embed glass fibre matting so that
the resultant cured membrane is considerably toughened.[10]  Liquid membrane applied too thinly over a flat roof resulting in very early failure PVC (vinyl) membrane roofing[edit]Polyvinyl chloride (PVC) membrane roofing is also known as vinyl roofing. Vinyl is derived from two simple ingredients: fossil fuel and
salt. Petroleum or natural gas is processed to make ethylene, and salt is subjected to electrolysis to separate out the natural
element chlorine. Ethylene and chlorine are combined to produce ethylene dichloride (EDC), which is further processed into
a gas called vinyl chloride monomer (VCM). In the next step, known as polymerization, the VCM molecule forms chains, converting the gas into a fine, white
powder - vinyl resin - which becomes the basis for the final process, compounding. In compounding, vinyl resin may
be blended with additives such as stabilizers for durability, plasticizers for flexibility and pigments for color. Thermoplastic
is heat-welded seams form a permanent, watertight bond that is stronger than the membrane itself. PVC resin is modified with
plasticizers and UV stabilizers, and reinforced with fiberglass non-woven mats or polyester woven scrims, for use as a flexible
roofing membrane. PVC is, however, subject to plasticizer migration (a process by which the plasticizers migrate out of the
sheet causing it to become brittle). Thus, a thicker membrane has a larger reservoir of plasticizer to maintain flexibility
over its lifespan. PVC is often blended with other polymers to add to the performance capabilities of the original PVC formulation,
such as KEE - Keytone Ethylene Ester. Such blends are referred to as either a CPA - Copolymer Alloy or a TPA -
Tripolymer Alloy. Vinyl roofs provide an energy-efficient roofing option due to their inherently light coloring. While
the surface of a black roof can experience a temperature increase of as much as 50 °C (90 °F) under the
heat of the full sun, a white reflective roof typically increases only 5 to 14 °C (9 to 25 °F). Vinyl
membranes can also be used in waterproofing applications for roofing. This is a common technique used in association with
green, or planted, roofs. Flexible Thermo Polyolefin[edit]Flexible thermo polyolefin is the exact physical and chemical name given to the product commonly known in the industry
as TPO (thermoplastic olefin). Although TPO exhibits the positive characteristics of other thermoplastics, it does not have
any plasticizers added to the product like other thermoplastics. This mis categorization made sense when the product was introduced
in the early 1990s and was unproven in the industry. TPO was categorized with thermoplastic membranes that were similar in
look and performance but were far from their real chemical and physical characteristics of the TPO membrane. Having no plasticizers
and chemically being closer to rubber but having better seam, puncture, and tear strength, TPO was touted to be a white weldable
rubber of the future. From 2007-2012, reported sales of TPO roofing products by all six major U.S. manufacturers showed materials
and accessories sales quadrupling those of all other flat roofing materials.[11] Thermoplastic polyolefin (TPO) single-ply roofing is the single most popular type of commercial low-slope roof covering as of 2016.[12] A TPO roof membrane consists of three layers: a TPO polymer base, a polyester reinforcement scrim middle layer,
and a TPO polymer top ply, which are heat-fused at the factory. TPO roof membranes typically come in three standard thicknesses:
45-mil, 60-mil, and 80-mil. Standard TPO membrane colors are white, grey, and tan, with custom colors also available from most manufacturers.
The most popular color for a TPO roof is white, due to the reflective, "cool roof" properties of white TPO. Using white roofing material helps reduce the "heat island effect" and solar heat
gain in the building. A TPO roof system can be fully adhered, mechanically fastened, or ballasted, although TPO roof systems
are rarely ballasted, since the ballast covers up the surface of the roof and negates the reflective property of white TPO.
TPO seam strengths are reported to be three to four times higher than EPDM roofing systems. This is a popular choice for "green"
building as there are no plasticizers added and TPO has very low degradation under UV radiation.[13] Thermosets[edit]Thermoset roof systems are typically EPDM (ethylene propylene diene monomer) rubber. EPDM is easily formed around
shapes like corners and is extremely resistant to ozone, ultraviolet light, weathering, high heat, and abrasion damage, making
it an excellent roofing material. EPDM membranes are seamed using pressure-sensitive tapes to join two sheets together.[14] Coal-tar pitch built-up roof[edit]Coal tar is an aromatic hydrocarbon and a by-product from the coking process of the coal industry. It is historically in abundance
where coal is used in steel manufacturing. It ages very slowly through volatilization and is an excellent waterproofing and
oil resistant product. Roofs are covered by heating the coal tar and applying it between layers of tar paper. It is typically limited to applications on dead level or flat roofs with slopes of 1⁄4 in 12 (1:48) or less.
It is the only roofing material permitted by the International Building Code to be applied to slopes below 1⁄4 in 12; the code allows its use on roofs with slopes as low as 1⁄8 in
12 (1:96).[15] It has a tendency to soften in warm temperatures and "heal" itself. It is typically surfaced with gravel
to protect the roof from UV rays, hail, and foot traffic, as well as for fire protection. Coal tar provides an extremely long
life cycle that is sustainable and renewable. It takes energy to manufacture and to construct a roof with it but its proven
longevity with periodic maintenance provides service for many years, with ages from 50 to 70 years not uncommon, with some
now performing for over a century. Currently, there are cold process (no kettle is used) coal tar pitch products that almost
eliminate all fumes associated with its typical hot process version. Coal tar pitch is often confused with asphalt and asphalt with coal tar pitch. Although they are both black and both are melted in a kettle when used in roofing,
that is where the similarity stops. Glass-reinforced plastic[edit] GRP fiberglass flat roofing A glass-reinforced plastic (GRP) roof is a single-ply GRP laminate applied in situ over a good-quality
conditioned plywood or oriented strand board (OSB) deck. The roof is finished with pre-formed GRP edge trims and a coat of
pre-pigmented topcoat. The durability and lightweight properties of GRP make it the ideal construction material for
applications as diverse as lorry aerofoils and roofs, boats, ponds and automotive body panels. GRP is also used in hostile
industrial settings for applications such as tanks and underground pipes; this is due to its ability to withstand high temperatures
and its resistance to chemicals. Unlike other roofing materials, GRP is not really a roofing material and has properties
that render it better suited to small craft construction. It is often used on small domestic installations, but usually fails
prematurely when used on larger projects. As well as being an inexpensive material, it is robust, inflexible and will never
corrode. Metal flat roofing[edit]Metal is one of the few materials that can be used for both pitched roofs and flat roofs. Flat or low-slope roofs
can be covered with steel, aluminum, zinc, or copper just like pitched roofs. However, metal shingles are not practical for
flat roofing and so roofers recommend standing-seam and screw-down metal panels. While metal can be an expensive option in
the short term, superior durability and simple maintenance of metal roofs typically saves money in the long term. A study
by Ducker International in 2005 identified the average cost per year of a metal roof to be US$3.2 per square metre ($0.30/sq ft)
while single-ply roofs stood at $6.1/m2 ($0.57/sq ft) and built-up roofing at $4.0/m2 ($0.37/sq ft).[16] Metal roofs are also one of the most environmentally sound roofing options, with most metal roofing material already
containing 30-60% recycled content, and the product itself being 100% recyclable. The value of recyclable scrap metal can
also provide a benefit to the homeowner; upon roof replacement, scrap metal from the old roof can be sold to recoup a potentially
large share of original material costs. Benefits, and uses, and drawbacks[edit] A rooftop in Haikou, Hainan, China, being used as a garden, storage area for wood, chicken run, and barbecue area A flat
roof is the most cost-efficient roof shape as all room space can be used fully (below and above the roof). Having a smaller
surface area, flat roofs require less material and are usually stronger than pitched roofs.[citation needed] This style roof also provides ample space for solar panels or outdoor recreational use such as roof gardens. Applying a tough waterproofing membrane forms the ideal substrate for green roof planting schemes. Where gable roofs are uncommon or space is limited, flat roofs may be used as living spaces,
with sheltered kitchens, bathrooms, living and sleeping areas. In third world countries, such roof tops are commonly used
as areas to dry laundry, for storage, and even as a place to raise livestock.[17] Other uses include pigeon coops, helipads, sports areas (such as tennis courts), and restaurants outdoor seating.[18] While flat roofs are usually designed to shed water, they may still be prone to water ponding, such as from snowmelt.[19] Flat roofs are also more prone to uplift from high winds than are hip or mansard roofs.[20][21] Maintenance and assessment[edit]A flat roof lasts longer if it is properly maintained. Some assessors use 10 years as an average life cycle, although this is dependent on the type of flat roof system in place.
Some old tar and gravel roofers acknowledge that unless a roof has been neglected for too long and there are many problems
in many areas, a BUR (a built up roof of tar, paper and gravel) will last 20-30 years. Despite these assessors, the actual
averages when studied come closer to 12-27, depending on the roof type, with some roofs lasting as long as 120 years. There
are BUR systems in place dating to the early 1900s.[citation needed] Modern cold applied liquid membranes have been durability rated by the British Board of Agrément (BBA) for 30 years. BBA approval is a benchmark in determining the suitability of a particular fiberglass roofing system.
If standard fiberglass polyester resin is used such as the same resin used in boat repairs, then there will be problems with the roof being too inflexible
and not able to accommodate expansion and contraction of the building. A fit-for-purpose flexible/elastomeric resin system
used as a waterproofing membrane will last for many years with just occasional inspection needed. The fact that such membranes
do not require stone chippings to deflect heat means there is lower risk of stones blocking drains. Liquid applied membranes
are also naturally resistant to moss and lichen. General flat roof maintenance[22] includes getting rid of ponding water, typically within 48 hours. This is accomplished by adding roof drains or scuppers for a pond at an edge or automatic siphons for ponds in the center of roofs. An automatic siphon can be created with an inverted ring-shaped sprinkler, a garden hose, a wet/dry vacuum, a check valve installed in the vacuum, and a digital timer. The timer runs two or three times a day for a minute or two to start water
in the hose. The timer then turns off the vacuum, but the weight of water in the hose continues the siphon and soon opens
the check valve in the vacuum. The best time to address the issue of ponding water is during the design phase of a new roofing
project when sufficient falls can be designed-in to take standing water away. The quicker the water is got off the roof, the
less chance there is for a roof leak to occur. All roofs should be inspected semi-annually and after major storms. Particular
attention should be paid to the flashings around all of the rooftop penetrations. The sharp bends at such places can open
up and need to be sealed with plastic cement, mesh and a small mason's trowel. Additionally, repairs to lap seams in the base flashings should be made. 90% of all roof leaks and failure occur at the flashings. Another important maintenance item, often
neglected, is to simply keep the roof drains free of debris. A clogged roof drain will cause water to pond, leading to increased
"dead load" weight on building that may not be engineered to accommodate that weight. Additionally, ponding water on a roof can freeze. Often, water finds its way into a flashing
seam and freezes, weakening the seam. For bitumen-based roof coverings maintenance also includes keeping the tar paper
covered with gravel, an older method, currently being replaced with bituminous roofing membranes and the like, which must be 'glued' in place so wind and waves do not move it causing scouring and more bare spots. The glue can be any exterior grade glue like driveway coating. Maintenance also includes fixing blisters (delaminations) or creases that may not yet be leaking but will leak over time. They may need experienced help as they
require scraping away the gravel on a cool morning when the tar is brittle, cutting open, and covering with plastic cement
or mastic and mesh. Any moisture trapped in a blister has to be dried before being repaired. Roof coatings can be used to
fix leaks and extend the life of all types of flat roofs by preventing degradation by the sun (ultra-violet radiation). A
thickness of 0.75 millimetres (30 mils) is often used and once it is fully cured, a seamless, watertight membrane is created. Infrared thermography is being used to take pictures of roofs at night to find trouble spots. When the roof is cooling, wet spots not visible
to the naked eye, continue to emit heat. The infrared cameras read the heat that is trapped in sections of wet insulation. Cool
roofs[edit]Main article: Cool roofRoofing systems that can deliver high solar reflectance (the ability to reflect the visible, infrared and ultraviolet wavelengths of the sun, reducing heat transfer to the building) and high thermal emittance (the ability to release a large percentage of absorbed, or non-reflected solar energy) are called cool roofs. Cool roofs fall into one of these three categories: inherently cool, green planted roofs or coated
with a cool material. - Inherently cool roofs: Roof membranes made of white or light colored material are inherently
reflective and achieve some of the highest reflectance and emittance measurements of which roofing materials are capable.
A roof made of thermoplastic white vinyl, for example, can reflect 80% or more of the sun's rays and emit at least 70%
of the solar radiation that the building absorbs. An asphalt roof only reflects between 6 and 26% of solar radiation, resulting
in greater heat transfer to the building interior and greater demand for air conditioning - a strain on both operating
costs and the electric power grid.[23]
- Green planted roofs: A green roof is a roof that is partially or completely covered with vegetation and a growing
medium, planted over a waterproofing membrane. A green roof typically consists of many layers, including an insulation layer;
a waterproof membrane, often vinyl; a drainage layer, usually made of lightweight gravel, clay, or plastic; a geotextile or
filter mat that allows water to soak through but prevents erosion of fine soil particles; a growing medium; plants; and, sometimes,
a wind blanket. Green roofs are classified as either intensive or extensive, depending on the depth of planting medium and
amount of maintenance required. Traditional roof gardens, which are labor-intensive and require a reasonable depth of soil
to grow large plants are considered intensive, while extensive green roofs are nearly self-sustaining and require less maintenance.
- Coated
roofs: One way to make an existing or new roof reflective is by applying a specifically designed white roof coatings (not
simply white paint) on the roof's surface. The coating can be Energy Star rated. Reflectivity and emissivity ratings for
reflective roof products available in the United States can be found in the Cool Roof Rating Council website.[24]
Cool roofs offer both immediate and long-term savings in building energy costs. Inherently cool roofs,
coated roofs and planted or green roofs can: - Reduce building heat-gain, as a white or reflective roof typically
increases only 5-14 °C (9-25 °F) above ambient temperature during the day
- Enhance the life expectancy
of both the roof membrane and the building's cooling equipment.
- Improve thermal efficiency of the roof insulation;
this is because as temperature increases, the thermal conductivity of the roof's insulation also increases.
- Reduce
the demand for electric power by as much as 10 percent on hot days.
- Reduce resulting air pollution and greenhouse
gas emissions.
- Provide energy savings, even in northern climates on sunny (not necessarily "hot") days.
See
also[edit]References[edit]- ^ Harris, Cyril M.. "Flat roof". Harris dictionary of architecture & construction.
3rd ed. New York: McGraw-Hill, 2000. Print.
- ^ National Roofing Contractors Association (Technical Library)
- ^ Passmore, Augustine C.. "Twenty Styles of Architecture". Handbook of technical terms used
in architecture and building and their allied trades and subjects,. London: Scott, Greenwood, and Co.;, 1904. 360. Print.
- ^ "Protected Membrane Roof Systems". Retrieved 2014-11-09.
- ^ Watts, Mike (May 2000). "PMR Systems: The Forgotten Solution" (PDF).
- ^ Lembeck, Henry G.. "Composite Design of Open Web Steel Joists". Washington University Department
of Civil Engineering, 1965
- ^ "Where Is Hypalon Among Today's Roofing Options?". www.buildings.com. Retrieved 2018-06-17.
- ^ "Roofing Systems | WBDG Whole Building Design Guide". wbdg.org. Retrieved 2018-06-15.
- ^ "Market for liquid applied membranes". Liquid - the market. Liquid Roofing and Waterproofing Association. Retrieved 13 September 2011.
- ^ "Liquid-applied waterproofing membrane for roofs" (PDF). European Patent EP 2 966 103 A1. January 2016.
- ^ "Thermoplastic Polyolefin (TPO) Roofing Systems". Buildings. Retrieved 2022-04-29.
- ^ "NRCA Releases 2015-16 Market Survey". Roofing Magazine. Retrieved 28 October 2022.
- ^ Gray, Jack. "TPO Roofing: Guide for Non-Roofers". Roof Online. Retrieved 28 October 2022.
- ^ SPRI (2019-01-09). "Single-Ply Roofing 101". SPRI. Retrieved 2022-04-29.
- ^ "Minimum Acceptable Roof Pitch by Material". Roof Online. Retrieved 2020-08-07.
- ^ "Low Slope Roofs". Archived from the original on 2015-08-16.
- ^ Reel, Monte (2006). "Up on the Roof". The Washington Post. Retrieved 21 August 2014.
- ^ Murano, Grace (20 October 2011). "10 Coolest Rooftop Attractions". Oddee. Retrieved 21 August 2014.
- ^ "Risk Management Series: Snow Load Safety Guide" (PDF). fema.gov. FEMA. p. 2-3. Retrieved 29 April 2022.
- ^ "Home Builder's Guide to Coastal Construction: Technical Fact Sheet Series" (PDF). fema.gov. FEMA. p. 10. Retrieved 29 April 2022.
- ^ Grazulis, Thomas P. (1993). Significant tornadoes, 1680-1991. St. Johnsbury, Vt.: Environmental
Films. p. 106. ISBN 1-879362-03-1.
- ^ "Your Guide to Home Maintenance - Flat Roofs" (PDF). Gateshead.gov.uk. Archived from the original (PDF) on 4 October 2013. Retrieved 1 October 2013.
- ^ Konopacki and H. Akbari (June 2001). "Measured Energy Savings and Demand Reduction from a Reflective Roof Membrane on a Large Retail Store in Austin". Lawrence Berkeley National Laboratory, Environmental Energy Technologies Division.
- ^ "Cool Roof Rating Council". Retrieved 13 March 2013.
External links
Flat Roof Specialist, flat roof renewal, flat roof overhaul, flat roof replacement, flat roof installing, flat
roof installer, flat roof installers, flat roof bonding, flat roof supplying, flat roof removal, flat roof skylights, flat
roof ventilation, flat roof covering, flat roof guarentee, flat roof felt, flat roof torch on, flat roof torch on felt, mimeral
flat roof, flat roof solutions, flat roof repairer, flat roof supplier, flat roofing specialists, flat roof advice, flat roofing
service, flat roofing experts, flat roofing replacement, flat roofing insulation, flat roof decking, flat roof joists, flat
roof supports, flat roof upstands
RooferFrom Wikipedia, the free encyclopedia Jump to navigationJump to searchFor someone who rides the
roof of a train, see atapper.  A German roofer installing a reed roof (he is wearing the traditional vestand trousers of a crafts person) A roofer, roof
mechanic, or roofing contractor is a construction worker who specializes in roof construction. Roofers replace, repair, and install the roofs of buildings, using a variety of materials, including shingles, bitumen, and metal. Roofing work can be physically demanding because it involves heavy lifting, as well as climbing, bending, and kneeling,
often in extreme weather conditions.[1] Throughout the world[edit] Roofers on a pitched roof in the United States conducting a roof tear-off In Australia this type of carpenter is called a roof carpenter and
the term roofer refers to someone who installs the roof cladding (tiles, tin, etc.). In the United States and Canada, they're often referred
to as roofing contractors or roofing professionals. The most common roofing material in the United States is asphalt shingles.
In the past, 3-tab shingles were used; nowadays, "architectural" or "dimensional" shingles are becoming
very popular.[2] Depending on the region, other commonly applied roofing materials
installed by roofers include concrete tiles, clay tiles, natural or synthetic slate, single-ply (primarily EPDM rubber, PVC, or TPO), rubber shingles (made from recycled tires), glass, metal panels or shingles, wood shakes or shingles, liquid-applied, hot
asphalt/rubber, foam, thatch, and solar tiles. "Living roof" systems, or rooftop landscapes, have become increasingly
common in recent years in both residential and commercial applications.[3][4] In the United States, regulation of the roofing trade is left
up to individual states. Some states leave roofing regulation up to county-level and municipal-level jurisdictions.[5] In California, for example, the California Contractors State License Board licenses and monitors
roofing contractors.[6] Unlicensed contracting of projects worth over a set threshold may result in stiff fines or even time
in prison.[7] In Oklahoma roofers are required to meet insurance and roofing license guidelines. Roofers are also
required to show their license number on their marketing material. The
United Kingdom has no legislation in place that requires a roofer to have a license to trade, although some do belong to recognized
trade organizations.[citation needed] Types of roofers[edit]There are four main types
of roofers: shinglers, who primarily install shingles, shakes, tiles, and other nail-on products on roofs with 5:12 pitches
or above; metal roofers, who focus on metal panels; single-ply or "flat" roofers, who focus on roofs such as single-ply
or foam roofs; and "hot" roofers, who work using tar-based products. It is not uncommon, however, for companies
to have their roofers service multiple styles and types of roofing; and certain manufactures will allow only pre-approved
installers, thus making these four roofer types limiting. As per the application areas, roofing contractors can be categorized
as Industrial or commercial roofers, Factory Shed roofers, Residential Roofers, Commercial roofers. Based on the types of
the materials, roofing can be classified as terrace roofing, metal roofing, polycarbonate roofing, steel roofing, PVC roofing,
skylight roofing. Pre-engineered companies installs roofing. See also[edit]
Kettyle / Articles / Flat Roofing - 1
- 2
- 3
- 4
- 5
- 6
- 7
- 8
- 9
- 10
- 11
- 12
- 13
- 14
May 21, 2013 PaddyArticles, Building materials, Flat roofing Flat roofingThis article covers: All types of flat roofing - Felt roofing
- Mastic asphalt
- Glass fibre
- Lead
- Other
metals
Torch on Felt for flat roofingTorch on Felt membrane roofing is now the most popular system used
for flat roofing As the title suggests, the technique involves heating a layer of bitumen that has been applied to the
felt using a Propane gas torch, which melts the bitumen allowing it to bond to the substrate or under layers of felt previously
applied. Together the layers form a flat roofing system. Traditionally the roll and pour method for felt flat roofing was
used. This involved heating Bitumen in a specially designed boiler and transporting it to the roof in buckets.  Torch on felt membranes  The roll and pour method and still the Rolls Royce of installation & requires great skill -Note thumbs facing forward
to avoid rolling hands into the hot bitumen @ 410 deg F
It would then be poured out and the felt
rolled over the molten bitumen. This type of application is very specialised and dangerous and a major influence
for the introduction of Torch on Felt. This application is far easier to use and subsequently has allowed installation to
be carried out by inexperienced people. The correct installation of flat roofing is a skilled art and should only be carried
out by suitably skilled contractors, so many of the problems associated with flat roofing are due to incorrect installation.
Installed correctly with modern high tensile felt membranes, there is no reason why a flat roofing felt system should not
last just as long as a tiled roof. Whilst the advantages of having a Torch on Felt flat roofing system installed are
obvious, there is a lot of choice on the market that can cause confusion. Some of these options available include torch-on,
self adhesive, pour and roll and glass fibre membranes. Any roofing company will be able to give you professional
roofing advice on the right type of flat roofing membrane for your property. Torch-on membranes can be applied to a
wide range of flat roofing scenarios in a relatively straightforward manner. Felt flat roofing is generally applied
in four layers comprising of: - A vapour barrier - Normally glass fibre based
- Insulation
layer - Closed cell ridged board in varying thicknesses.(Not applicable in all cases)
- Intermediate layer
- Cap
sheet
Torch-on membranes are extremely effective and can provide you with a good quality roof for years to come.
However, applying these can be dangerous and it is essential to consult a professional construction company if you are thinking
about having one of these installed. Enlisting the help of professionals will ensure that the job is carried out correctly,
whilst it will also prevent you from potential injury Vapour barriers are applicable to all flat roofing
systems.A properly installed flat roofing system should include a vapour control layer. A vapour control
restricts water vapour from the dwelling damaging the insulation in a warm deck scenario ie: where the insulating material
is fitted to the roof decking. Over time condensation can also cause any timber or support joists to rot. Replacing
this is an extremely costly procedure, so to avoid this problem a vapour barrier control layer and insulation should
always be fitted in your flat roofing system. If you are fitting insulation between the roof joist then its imperative
that the space is kept well ventilated. A build up of condensation over long periods can cause the timer structure to rot. The vapour control
layer is the first layer of the flat roofing to be installed. It is installed directly to the roof decking and should be fixed
to the decking with clout head nails and sealed on the laps and perimeter. Few are aware of the importance of this layer,
but when you consider the amount of moisture that can build up in a standard house you'll understand why these are necessary.
A typical family home with two adults and two children living under normal conditions can create up to ten Litres of
moisture over a 24 hour period. The moisture or water vapour has to go somewhere, and unfortunately not enough properties
are adequately ventilated or insulated correctly to deal with this. The list below highlights some factors that may
indicate that your property is at risk from poor ventilation. - Noticeable vapour in the inside of
your property
- Moisture in building materials
- Moisture build-up on the floor, windows, or the walls of your
property
- Black mould usually on external walls
Excessive vapour and condensation build
up is more common in some properties than others. Older buildings usually have walls without insulation or cavities, and traditionally
they had adequate ventilation from chimneys, draughty windows and doors. With modern living, home owners seal up the chimneys,
fit sealed double glazed windows and doors, and the roof, more often than not, will have been renewed with a non permeable
felt underlay. These new developments cut out all the previous forms of ventilation and heat the property during the
winter months. The warmer air will carry higher levels of moisture. Air will shed this excess moisture when it meets
a cold surface. This is called the dew point. Properties with swimming pools will be exposed to particularly high levels of
water vapour. Some rooms of every property are also more susceptible to vapour damage than others. Kitchens
and bathrooms, for example, are more likely to suffer from problems with condensation. Controlling moisture in a property
is very important. Specialist building contractors will be able to assist and make recommendations. If your property meets
any of the criteria that has been highlighted in this article, it is best to get professional help immediately, as delaying
it could make matters worse. Self-Adhesive felt for flat roofing.A self adhesive membrane is perhaps the easiest
roofing material to apply for flat roofing. The underside of this membrane uses soft bitumen to form a bond to the substrate
or under layer. This makes the use of blow torches and bitumen redundant, and is typically used by the DIY enthusiast. It
is fine for the use on outbuildings, sheds etc, however for more important applications it is better to use an alternative
flat roofing option installed by a specialist.  Self adhesive flat roofing When it comes to Bituminous flat roofing there are generally two main choices. These
choices are either, Asphalt or a Felt membrane roof. Although in previous years asphalt and was seen as extremely
popular choice for all types of flat roofing , it is expensive and a high skill level is required to apply it correctly. Roofing
technology has moved on and now felt membrane roofs are seen as the better choice for flat roofing as they offer
a number of advantages. These advantages are listed below: - They require little maintenance
and have a long life span iof installed correctly.
- Cheaper andeasierto apply than other flat roofing materials
Even though felt flat roofing is easier to apply when compared to other types, roofing is not a job that should be carried
out by a DIY enthusiast. It is a job that involves many risks and ideally you should speak to a professional roofer who will
be able to carry out this task in a safe and efficient manner. Once you have spoken to a professional construction company,
it is likely that you will be presented with a number of membrane options. These options can include torch-on, pour and
roll, glass fibre and self adhesive membranes. The choice here can be overwhelming for some. But before you
make your mind up, ask a professional contractor who will be able to provide you with invaluable roofing advice whilst carrying
out this skilled and potentially dangerous task. Felt flat roofing. The roll and pour method.For use by the
specialist installer.  The roll and pour method Pour and roll membranes are applied onto roofs by using hot bitumen. Bitumen is bi product
of the petrol refining industry. Bitumen is supplied in 25kg blocks or tubs it is then usually broken up on site
and heated in a specialist boiler until it is molten. Once at the correct temperature it is ladled into buckets- some boilers
have taps to ease this process. The felt for flat roofing is set out and cut to length. It is then rolled back-
One operative will pour the molten bitumen on to the surface and the other will roll the felt over allowing the
bitumen to squeeze out of each side. The surplus is then wiped over with wallpaper stripper. The finish layer will usually
have a mineral or slate chipped finish impregnated into the surface of the felt. Keeping this free of surplus bitumen. Using
a roll and pour method is very skilled- that's why most companies that install flat roofing will now only use
a torch on felt systems. Most modern operatives wouldn't now know how to roll and pour a final mineral surface top
layer. A rolled and poured roof is the king of felt roofing. The bond created is arguably stronger than the bond that is created
when using a self adhesive or torch on membrane, but there are some drawbacks. Applying a membrane in this way is
a skilled technique that will require the use of a professional roofer. There are fewer companies now who have the skills
and equipment to carry out this type of installation, and it is more expensive, but applied correctly it is the Rolls Royce
of felt roofing. There are a number of roofing companies that will be able to provide high quality services at competitive
rates, whilst also ensuring that your roofing membrane is fitted correctly. The demise and bad name associated
with felt flat roofing In some ways its quite sad but the roll and pour method was also responsible for the
demise and poor name flat roofing has suffered. With the rising cost of bitumen many installers started to apply the bitumen
using cotton floor mops so spreading it more thinly and saving money. This process caused a hit and miss bonding between the
layers and a weakness in the overall system allowing water to permeate between the layers and causing leaks. Pour and
roll membranes for flat roofing will typically use three layers of felt membrane, and a final layer which is referred to as
the cap sheet and will normally have a granular finish available in different colours. It can be argued that this is
the best option if you are thinking about investing in a new flat roof. This of course will save you money in the long run.
Companies who can undertake this type of installation properly are few and far between. Mastic Asphalt for flat roofingMastic
asphalt is a waterproof material that is used for flat roofing, also used on floors, paving and basements, but most commonly
on flat roofing. Not often now seen due expense and modern easier to apply alternatives. Asphalt is made up of a compound
called bitumen. Bitumen is a by-product of the petroleum refinement stage, and within this compound the particles are bound
together especially tight. In In order to add additional strength to mastic asphalt, fine aggregate is blended in. Aggregate
types can vary dependant on use but often limestone is used for roofing grades and granite is added for paving use.
This material is known as mastic asphalt.  Mastic Asphalt Roofing Mastic asphalt is a building material that has a number of uses. It is used on pavements and
flooring, but most importantly it is used in flat roofing. It is commonly used on the flat roofing of commercial buildings
as it can create an extremely strong and durable roof that will accept traffic without causing damage. However point loading
in very warm conditions is not recommended. Mastic asphalt for flat roofing is generally applied in two coats. The material
is supplied in solid blocks and is heated using a specialist boiler or mixer. It is poured onto the surface and, using
a hard wood float, it is spread to the correct thickness. The second coat has dry sand applied to the top that is rubbed in.
When it cures, a dense and solid material is created which is waterproof and impermeable. The benefits of a mastic asphalt
roof are obvious, but they still need to be installed correctly for them to reach their full potential. This article will
look at some of the regulations and guidelines that are associated with mastic asphalt flat roofing, which need to be followed
to ensure a professional finish. When Applying Mastic Asphalt for flat Roofing GenerallyMastic asphalt needs
to be applied in accordance with the traffic conditions and requirements of the roof. - Where falls are more than
1:80, two 20mm coats of mastic asphalt are required
- Where falls are below 1:80, three thinner layers of mastic asphalt
will be required generating no more than 30mm. These guidelines are in accordance with the BS 8218: 1998 regulations. When
Applying Mastic Asphalt to Horizontal, Vertical or Sloping Surfaces
- On horizontal surfaces and pitches up to 10°,
two 20mm coats of mastic asphalt will need to be applied on a separating membrane
- On sloping and vertical surfaces
over 10°, three 20mm coats will need to be applied without a separating membrane
- On sloping and vertical surfaces
over 10° which use timber or lightweight concrete, but not skirting, three coats of mastic asphalt that create a combined
thickness of 20mm are required with no separating membrane
- On sloping and vertical surfaces over 10° which use
timber or lightweight concrete, which includes skirting, three coats of mastic asphalt that create a combined thickness of
20mm needs to be laid onto metal lathing over a separating membrane
- On horizontal surfaces that are used as reservoirs,
roof gardens or buried waterproofing, three coats of mastic asphalt that create a combined thickness of 30mm needs to be applied
onto a glass fibre tissue membrane
Vapour Barriers for flat roofing- Vapour
barriers need to be laid onto a glass fibre tissue. A minimum 10mm vapour barrier thickness is required
Up-stands
and skirting for flat roofing- On up-stands or skirting that is not timber or lightweight concrete and is below
300mm in height, two coats of mastic asphalt are required to create a combined thickness of no less than 13mm
- On up-stands
or skirting that is not timber or lightweight concrete and is above 300mm in height, three coats of mastic asphalt are required
to create a combined thickness of no less than 20mm
- Two coats may be acceptable in areas that are not exposed to the
outside, for example, tanking rooms or mechanical service areas
- On up-stands or skirting that is timber and lightweight
concrete, three coats of mastic asphalt are required to create a combined thickness of 20mm. This needs to be applied on expanded
metal lathing using a separating membrane
- On up-stands and skirting which has expanded metal lathing that is attached
to concrete, brickwork or block work, three coats of mastic asphalt to a combined thickness of 20mm will need to be applied.
This includes a separating membrane.
These are the requirements that are outlined in the BS 8218:1998 guidelines
which should be followed if you want to obtain a safe, durable and legal roof. A decent roofing company will be able to abide
by these regulations, and if you want a roof that is fitted professionally it is advisable to use a company that has relevant
experience. Glass Fibre Roofing ( GRP ) for flat roofingWhether you need a new roof to replace a damaged one,
or you are thinking about creating a new build, installing a roof will mean making a desision about what type is best. No
roofs come cheap and the choice you make needs to be viewed as an investment. This important decision will affect the future
salability of your property, so it is paramount that the right option is chosen. Fibreglass flat
roofing is an ideal choice for properties that have extensions or garages. Traditionally felt or asphalt is the material of
choice for flat roofs, but since technology has advanced this no longer seen as the only option. Glass fibre is very durable
and requires little maintenance and is a perfect choice for flat roofing.  Glass fibre roofing being installed Benefits for using GRP for flat roofing that are highlighted below:- Extremely durable and hardwearing
- Can be exposed to all weather types
- A life-span
that outlives many other flat roofing materials - a typical fibreglass roof will last at least 25 years
- Requires
little maintenance and can be easily repaired if necessary
- A cheaper option to some flat roofing alternatives like
lead, which means fibreglass is not a material that will be targeted by thieves
- Can be overlaid with tiles to form
a patio or roof garden
Fibreglass roofs are also known as GRP (glass reinforced plastic). When installed
layers of fibreglass matting are bonded in a two part resin it is then finished with a gel coat or top-coat that can be coloured
to your specific choice. This top-coat is applied to the fibreglass roofing layer which promotes additional water resistance
and durability. Top-coats and fibreglass roofing systems should be installed by a professional roofer for optimal results,
but if you feel brave then you can use the information in this article to try and install a GRP roof yourself. However, it
must be mentioned that installing a GRP without any knowlege of roofing or glass fiber is beyond the scope of most people.
Enlisting the help of a professional is probably a better option. For information purposes however, a rough overview as to
how a fibre glass flat roofing system is installed is outlined below.  This is what a completed glass fiber roof can look like Assuming that the structure of the roof has plywood boards
laid securely over the joists, a GRP roof can be installed. GRP cannot be fitted in conditions below 5°C and ideally this
sort of task should only be undertaken during dry warm weather. Fibre glass matting is applied to the 18mm plywood boards,
and then a specialist resin is applied using a roller or brush. Whwn this has cured a second layer of matting is applied .This
adds to its durability and water resistance and is vital if you want to be able to get the best out of your new fibreglass
roof. Upstands can be formed using strips of matting and drips or cappings can be bought purpose made and incorperated into
the GRP flat roofing system. Finally a coloured top gell coat is applied to complete the flat roofing system. As the
bullet points below suggest, gaining a GRP roof is a popular option if you're looking at having a flat roofing system
installed on your property. Under most circumstances two experienced roofers can strip, re-deck, laminate and apply
a top-coat to a roof at a rate of around 10 square meters a day. Application of Fibre glass for flat RoofingA
fibreglass flat roof is a great alternative to traditional materials for flat roofing such as felt or asphalt. Asphalt
and felt are no longer seen as the flat roofing material of choice. Fibreglass is more durable and water resistant, whilst
its life span is longer and it usually works out to be more cost effective. This article however is not looking at the advantages
of fibreglass roofing, but it aims to provide some useful information that will come in handy when installing a GRP roof. When
laying any roof it is always advisable to check the weather conditions beforehand, but if you are going to fit a fibreglass
flat roofing system in the winter the following tips will come in useful. - Top-coating is essential to get the best
out of a GRP roof, but avoid doing this after 2pm in the winter. The heat from the sun is essential if the resin is to cure,
even when you have invested in a high quality top-coat that can cure at temperatures below 10°C
- When top-coating
it is a good idea to warm the resin. This can be achieved by leaving it in a warm room over night which will make it much
easier to apply the next day
- If it does start to rain, cover the roof with a waterproof sheet to protect it. Make
sure you have one on standby in the event of this happening
- If you are running out of time and have not yet applied
the fibreglass lamination layer, then coat the exposed plywood with a catalysed resin. This will protect wood from the elements
allowing you to continue work at a later date
- It is vital for the wooden substrate to be completely dry before it
is laminated with fibreglass. Trapped moisture will cause major problems
As already mentioned, the tips listed
above are useful for people who plan to lay a fibreglass flat roof in the winter. However, different techniques will have
to be employed if you plan on laying GRP flat roofing system in warmer months. These are outlined below. - Hot weather
can cause top-coating resin to dry quickly. Ideally small batches should be mixed up regularly, as opposed to mixing it all
at once
- A top-coating should not be applied when the temperature is above 35°
- If a roof is top-coated
in strong sunlight it will not be able to cure properly. It may be better to undertake this task later on in the day, which
will save you from having to do it twice
- Apply the fibreglass laminate in short runs. By doing this the resin is less
likely to catalyse and consequently have a negative impact on your roof
These tips regard the installation of
your fibreglass flat roofing system, but what about caring for the tools that you have used? Acetone is an essential
product for cleaning your tools. This can be applied to paintbrushes and polyester rollers, but not the bucket that you have
mixed your resin in. To keep this clean, coat the bottom of your bucket with resin. After it has cured it can be peeled out,
which makes it instantly clean for the next task. Under no circumstances is it advisable to wash your hands with acetone,
as it's a strong chemical that is dangerous to your skin.  Here is another example of a stylish fibre glass roof. These tips are useful if you are planning to fit a fibreglass
flat roofing system yourself, but for high quality results it is advisable to use a professional roofing company. Professional
roofers will have years of experience when it comes to undertaking tasks like this, and it is in their best interest as professionals
to install a roof that is functional, durable and attractive. Lead for flat RoofingRoofing materials come in
a variety of forms, but arguably the best traditional materials for flat roofing is lead. Most traditional roofs use lead
as it is an extremely durable material that can last for generations. It provides easy malleability when compared to other
metals and is ideal for guttering, flashings and bridging junctions. Although lead roofing can be expensive, it provides a
beautiful, timeless finish that is ideal for properties that want to maintain a traditional look and should not be overlooked
as a flat roofing system. Specialis Roofing companies will undertake this kind of work primarily using lead in that
are manafactured in 6m Rolls. The lead is laid and dressed onto timber boards which create a weatherproof surface all year
round, whilst their life span can last in excess of a hundred years. This technique has been applied to buildings throughout
the country for centuries and it remains a tried and tested roofing method.  Lead Roofing Lead sheets for flat roofing come in a variety of weights and sizes. Code numbers are used to determine
these differences in weight, and generally each sheet will be given a number between 1 and 7. This number refers to the weight
in pounds per square foot. So for example, code 6 basically means that the lead sheets weigh six pounds per square foot, and
this rule applies to each number. While lead roof work is generally undertaken on larger historic buildings, it can
also provide the same benefits for smaller modern properties. This has led to an increased popularity for flat roofing
in recent years, but there are some drawbacks that people need to be made aware of. Even though lead roofs are extremely durable,
they do have a tendency to "creep" down. This is due to the heavy weight of lead, and the heating and cooling effect
that the seasons can have on it. But despite this problem, lead roofing is still seen as the most durable and cosmetically
pleasing roofing material on the market. Like all roofing work, lead for flat roofing will have to be installed or maintained
by a professional. It is a skilled job with a number of inherent risks and so it is not something that should be undertaken
by a DIY enthusiast. If you feel that your property could benefit from the many advantages of lead roofing, speak to a professional
building contractor. Lead Sheet Lead is a building material that has been used in roofing for
centuries. It provides excellent levels of durability and water resistance, whilst guaranteeing a low maintenance roof that
is sure to last for generations. To have a lead roof installed properly, high quality lead sheet will have to be used. This
article will go on to look at a few specific details that need to be considered before purchasing or fitting lead sheet. The
majority of lead sheet will be described as "milled lead sheet". This term is used to describe the manufacturing
process that it undergoes in order to meet British standard building requirements. These building standards are highlighted
in the BS 1178 document, which states that all milled lead sheet will have to have a minimum chemical composition of 99.9%,
while it will also have to meet industry standard sizes. These sizes are given code numbers which represent the dimensions
of the lead sheet. The codes and their corresponding sizes are displayed in a table below. CODE NUMBER. | THICKNESS (mm). | WEIGHT(kg/m2) | THICKNESS(Decimal.) | THICKNESS(Nearest inches.) | WEIGHT(Lbs/sq ft.) | 3 | 1.25 | 14.18 | 0.049 | 3/64" + | 2.91 | 4 | 1.80 | 20.41 | 0.071 | 5/64"
- | 4.19 | 5 | 2.24 | 25.40 | 0.088 | 3/32" - | 5.21 | 6 | 2.50 | 28.36 | 0.098 | 3/32" + | 5.82 | 7 | 3.15 | 35.72 | 0.124 | 1/8" - | 7.33 | 8 | 3.55 | 40.26 | 0.140 | 9/64" - | 8.26 |
These
codes represent the diameters displayed above, but to make life easier they are also colour coded. These are as follows.
- 3 = Green
- 4 = Blue
- 5 = Red
- 6 = Black
- 7 = White
-
8 = Orange
The majority of lead sheeting in the UK will follow these dimensions and their corresponding colour
codes, but there will be times when larger pieces of lead sheet will be required. Typically these extra large sheets are created
to meet dimensions that measure up to 12m in length, by 2.40m in width. All lead sheets can alternatively be made to measure
by the manufacturer, but there will be times when thinner lead sheet is required. These thinner sheets are not usually used
in roofing, but they are sometimes used for X-ray protection and sound insulation. As a result these thinner lead sheets are
not colour coded and built to industry standard regulations, but they are often used as part of lead-cored bitumen felt which
is typically used to provide a high quality damp proof course. The standard measurements that lead sheeting comes in
(code No. 3-8) will usually meet all of your building and roofing needs. This will include flashings, weathering's, cladding
and the majority of all external lead work, but this is assuming that there are no additional factors that need to be accounted
for. For example additional thickness may be required to provide protection against thermal movement and mechanical damage,
while having a sufficient amount of metal when dressing, bossing or shaping lead will also need to be taken into consideration. Cast
Lead Sheeting for flat roofing.So far this article has looked at the typical dimensions and measurements that are
associated with lead sheeting, but little has been said about the various types available. Firstly there is "cast-lead"
sheeting. Cast lead sheeting is made using a tried and tested method that involves pouring molten lead over a bed of prepared
sand. In most cases this type of lead sheeting is used to replace older roofs, but as these are in decline, so is this type
of roofing material. Nevertheless this material continues to be in use in the UK, but as it's largely created in independent
manufacturing plants there are no set industry standards. This means that variations will occur, but generally sheets come
in sizes that correspond to code numbers 6, 7 and 8 on the milled lead sizing chart highlighted above. The texture and consistency
of this material will differ slightly when compared to more refined lead sheeting, but ultimately there are no real differences
with regards to its durability and its practicality. Machine Cast Lead Sheeting for flat roofingMachine cast
lead sheeting is another option that is available. As the name suggests, this type of lead sheeting is made by a machine which
allows for increased precision and regulated dimensions. Typically these sheets will come in sizes that vary between 0.4mm
- 1.2mm in thickness, while their maximum width will usually reach 1.2m. Lead Laminates for flat roofing and wall claddingFor
extra support, sound insulation and resistance to radiation, lead laminates are used instead of more conventional lead sheeting
types. Lead laminates use thinly milled lead sheeting which is laminated onto a board substrate such as plywood. The
combination of these materials essentially creates a panel that is useful for both flat roofing and external wall cladding.
These provide exceptional protection against thermal movement, but the bond between the outer material and the inner layer
of lead has to be strong in order for them to function properly. The strength of this bond is especially important if the
laminate panels are going to be used for external purposes, but for internal usage, this is less of an issue. Regardless,
it is always best to purchase them from a reputable company that specialises in making them. As we can see the main
choices for lead flat roofing are milled, cast lead, machine cast lead and lead laminates. All of these have a number of advantages
and disadvantages which will suit some properties better than others, but ultimately all of them will require similar accessories
and fittings. Ideally an experienced installer will fit the type of lead system that has been chosen, but regardless of who
fits it the following materials will be required. - Copper clips - all copper clips used should meet BS 2870 standards.
They need to be cut from a copper sheet no less than 0.6mm in thickness, while at a temper grade of ¼ H
- Nails
- all nails used need to be copper clout nails that conform to BS 1202 (part 2 table 2) industry standards. They need to be
a minimum of 25mm long, with a minimum shank diameter of 10SWG
- Screws - these need to be a minimum of 25mm long with
a diameter that doesn't exceed 10 SWG. These need to conform to BS 1210 regulations
- Solder - all solder used for
fixing dots, angles or seams will have to conform to BS 219 regulations. Grade D or grade J should be used
- Underlay
- this will depend on the surface that the underlay is fitted onto. Waterproof building paper that conforms to BS 1521 regulations
will be suitable for most construction work, assuming that the substrate surface is relatively even and smooth
So
while the lead sheeting used will have to meet BS 1178 regulations, the accessories used to fit it will also have to meet
the guidelines highlighted in the bullet points above. If the materials used do not abide by these guidelines, then any work
that has been carried out could be deemed illegal and unsafe. To ensure that these standards are met, always use a registered
construction company complete with the necessary insurance and qualifications. Now that the different types, standards,
dimensions and accessories of lead sheeting for flat roofing have been looked at in some detail, the actual properties of
lead as a material need to be considered. To start with, it is the softest of all common metals making it extremely malleable
and easy to shape. This can be done with hand tools and without risk of fracture, making it ideal for intricate aspects of
metal work. With regards to flat roofing, it is often used for flashings and areas that need to be fitted tightly to the surface
of a structure. A good example of this is a contoured region or a particularly challenging aspect of single-lap tiling. These
examples demonstrate the versatility that is associated with using lead as a roofing material, but to fully appreciate the
benefits of lead, more technical qualities need to be analysed.  note the precision work in the lead roofing details As lead sheets are predominately used as a roofing material it
is likely they will be exposed to the elements on a regular basis. This can have a big impact on lead, and it is not unusual
for it to be subjected to linear expansion. Linear expansion is the process that can cause any metal to expand and contract
when exposed to heat, and in lead's case this can easily occur at around 40 °C. Unfortunately this is a temperature
that can be reached on a hot day, and when this occurs lead can begin to crack. This is obviously a negative effect that can
distort a roof, but there are steps to be taken that prevent this. The linear expansion for lead is 0.0000297 at 1°C,
which means that a 2 meter sheet of lead could expand by about 2-3mm when exposed to heat. To stop this from happening and
subsequently reduce the levels of thermal movement, it is vital to fit lead sheeting in smaller pieces. Even though there
is no set industry standard that relates to the size of each sheet used and their susceptibility to thermal movement, there
will be manufacturer's recommendations. It is vital to follow these for a properly installed lead roof, and as a general
rule of thumb, the thinner the sheet the smaller the piece Copper for flat roofing and wall cladding.If you
want a flat roofing system that really stands out from the crowd whilst also offering superb durability and weather resistance,
then look no further than copper roofing. The colour of copper makes this metal seem unique when compared to other roofing
materials, and undoubtedly this is the reason why it is often chosen. The effect that copper roofing creates can be breathtaking,
especially as it can change over time, but they offer so much more than simply being cosmetically pleasing.  Copper sheet roofing Copper flat roofing systems are typically fitted using the standard seam technique. This technique
pays careful attention to the design of the roof, especially where chimneys and gullies are concerned. Once the layout of
the roof has been taken into consideration, copper sheets will be secured over a layer of asphalt which is attached to the
frame of the roof. The copper sheets will be secured by stainless steel clips, which are then welded between the up stands
of the copper bays. This is a task that needs to be carried out by a professional flat roofing company that specialises in
this type of flat roofing material . While there are advantages of a copper roof over more conventional materials, the
main reason why they are usually considered typically boils down to aesthetics. Copper roofs add elegance and class to any
property, and if money wasn't an issue they would be the first choice for a lot of people. Zinc for flat roofing
and wall cladding.Metal roofing materials are becoming increasing popular for flat roofing. Traditionally lead and
copper can be extremely expensive. Zinc roofs provide an alternative that allow for similar levels of durability, whilst
retaining the benefits that they create for generations but at less cost  Zinc sheet roofing, For a classic contemporary look. As a flat roofing material, zinc is extremely versatile. it
can be adapted to cater for complex roof designs and wall cladding. If you are thinking about building or updating a
roof that contains either of these features, then perhaps zinc is a good choice for you. Fortunately there are specialist
roofing companies who are familiar with zinc flat roofing systems. Overall, zinc roofs are durable, require little maintenance
and have great longevity. They share a number of characteristics with copper, in that they both create patinas and are metal
based, but ultimately zinc provides a cheaper and more versatile option. Some people will argue that copper roofs are more
pleasing to the eye, but this of course is a matter of personal opinion. To gain a zinc roof with a high quality finish, make
sure that you enlist the help of a professional roofer. Roofing is not a task for DIY enthusiasts this type of flat roofing
requires a lot of skill and can be dangerous. Stainless-Steel for flat RoofingWhether you are creating a new
build or are updating a pre-existing property, metal roofing is an option that appeals to a wide audience. Metal roofing is
renowned for its attractive appearance, durability, fire resistance and overall charm, but there can be confusion due to the
number of materials available. Some of the more common options include zinc, copper and lead, but each of these have various
advantages and disadvantages that usually depend on individual circumstances. One metal flat roofing type that can make a
statement is stainless steel.  Stainless steel roofing. Tends to be used more as an industrial roof covering - Stainless steel is very light.
- Although
stainless steel doesn't create a patina like zinc and copper, the chromium in the metal provides a bright high reflective
finish- so if you want cool then look no further.
- Little maintenance is required
- Stainless steel is heat resistant
in nature. This means it provides an excellent level of fire resistance
- Assuming that the roof is erected with a continuous
seam running through it, the use of lightning conductors will be made redundant
- Stainless steel roofs have an extremely
long life span
- Can provide an attractive finish
As the list above shows, stainless steel for flat roofing
provides a number of advantages over more traditional materials such as tile, lead and asphalt. Whilst this is true a number
of these advantages also apply to metals such as zinc and copper. This is why there is often confusion with regards to the
type of metal that is best suited for a roof. Generally speaking metal flat roofing is a good option if you are looking
for a light long lasting, high quality and attractive finish. Copper can be expensive; but wow that patina is wonderful.
If you are unsure of where to start, take a look at the pictures and see what floats your boat. All matelic flat roofing systems
will be more expensive than other flat roofing types as the material used can be quite costly, and the techniques required
to install them are highly skilled. Both of these factors will add to an increased overall cost. However, this should not
be viewed in a negative light. The increased cost is also a sign of the increased quality that you are purchasing. A metalic
flat roofing system will last for generations, requiring little to no maintenance. If you like the idea of a metal flat
roofing system, but are still unsure as to what type would best suit your needs, then make an enquiry with a professional
roofing company. They will be able to provide you with invaluable roofing advice, whilst they will also be able to carry out
work in a safe and efficient manner wherever necessary. Image Credits: smaedli, Axelph and furious green cloud You may also like:
RoofFrom Wikipedia, the free encyclopedia Jump to navigationJump to searchA roof is
part of a building envelope. It is the covering on the uppermost part of a building or shelter which provides protection from animals and weather, notably rain or snow, but also heat, wind and sunlight. The word also denotes the framing or structure which supports that covering.[1] The characteristics of a roof are dependent upon the purpose
of the building that it covers, the available roofing materials and the local traditions of construction and wider concepts
of architectural design and practice and may also be governed by local or national legislation. In most countries a roof protects primarily against rain. A verandah may be roofed with material that protects against sunlight but admits the other elements. The roof of a garden conservatory protects plants from cold, wind, and rain, but admits light. A roof may also provide additional living space, for
example a roof garden. EtymologyOld English hrof "roof, ceiling, top, summit; heaven, sky," also figuratively,
"highest point of something," from Proto-Germanic *khrofam (cf. Dutch roef "deckhouse, cabin, coffin-lid,"
Middle High German rof "penthouse," Old Norse hrof "boat shed"). There are no apparent connections outside the Germanic family. "English alone has retained the word in a general
sense, for which the other languages use forms corresponding to OE. þæc thatch" [OED]. Design elementsThe elements
in the design of a roof are: The material of
a roof may range from banana leaves, wheaten straw or seagrass to laminated glass, copper (see: copper roofing), aluminium sheeting and pre-cast concrete. In many parts of the world ceramic tiles have been the predominant roofing material for centuries, if not millennia. Other roofing materials include asphalt, coal tar pitch, EPDM rubber, Hypalon, polyurethane foam, PVC, slate, Teflon fabric, TPO, and wood shakes and shingles. The construction of
a roof is determined by its method of support and how the underneath space is bridged and whether or not the roof is pitched.
The pitch is the angle at which the roof rises from its lowest to highest point. Most US domestic architecture, except in very dry regions, has roofs that are sloped, or pitched. Although modern construction
elements such as drainpipes may remove the need for pitch, roofs are pitched for reasons of tradition and aesthetics. So the
pitch is partly dependent upon stylistic factors, and partially to do with practicalities. Some types of roofing, for example thatch, require a steep pitch in order to be waterproof and durable. Other types of roofing, for example pantiles, are unstable on a steeply pitched roof but provide excellent weather protection at a relatively low angle. In regions where
there is little rain, an almost flat roof with a slight run-off provides adequate protection against an occasional downpour.
Drainpipes also remove the need for a sloping roof. A person that specializes
in roof construction is called a roofer. The durability of
a roof is a matter of concern because the roof is often the least accessible part of a building for purposes of repair and
renewal, while its damage or destruction can have serious effects. Form Terminology of some roof parts The shape of roofs differs
greatly from region to region. The main factors which influence the shape of roofs are the climate and the materials available
for roof structure and the outer covering.[2] The basic shapes of roofs are flat, mono-pitched, gabled, hipped, butterfly, arched and domed. There are many variations on these types. Roofs constructed of flat sections that are sloped are referred to as pitched roofs (generally if the angle exceeds 10 degrees).[3] Pitched roofs, including gabled, hipped and skillion roofs, make up the greatest number of domestic
roofs. Some roofs follow organic shapes, either by architectural design or because a flexible material such as thatch has
been used in the construction. Parts Star-roof lifted into the ESOSupernova Planetarium & Visitor Center. [4]There are two parts to a roof, its supporting structure
and its outer skin, or uppermost weatherproof layer. In a minority of buildings, the outer layer is also a self-supporting
structure. The roof structure is generally supported upon walls, although
some building styles, for example, geodesic and A-frame, blur the distinction between wall and roof. Support The roof of a library in SwedenThe supporting structure of a roof usually comprises
beams that are long and of strong, fairly rigid material such as timber, and since the mid-19th century, cast iron or steel. In countries that use bamboo extensively, the flexibility of the material causes a distinctive curving line to the roof, characteristic
of Oriental architecture. Timber lends itself to a great variety of roof shapes. The timber
structure can fulfil an aesthetic as well as practical function, when left exposed to view. Stone lintels have been used to support roofs since prehistoric times, but cannot bridge large distances. The stone arch came into extensive use in the ancient Roman period and in variant forms could be used to span spaces up to 140 feet (43 m) across. The stone arch or vault, with or without ribs, dominated the roof structures of major architectural works for about 2,000 years, only giving way
to iron beams with the Industrial Revolution and the designing of such buildings as Paxton's Crystal Palace, completed 1851. With continual improvements in steel girders, these became the major structural support for large roofs, and eventually for ordinary houses as well. Another form of girder is the reinforced concrete beam, in which metal rods are encased in concrete, giving it greater strength under tension. Outer layerThis part of the roof shows great variation dependent upon availability
of material. In vernacular architecture, roofing material is often vegetation, such as thatches, the most durable being sea grass with a life of perhaps 40 years. In many Asian countries bamboo is used both for the supporting structure
and the outer layer where split bamboo stems are laid turned alternately and overlapped. In areas with an abundance of timber,
wooden shingles and boards are used, while in some countries the bark of certain trees can be peeled off in thick, heavy sheets and used for roofing. The 20th century saw the manufacture of composition asphalt shingles which can last from a thin 20-year shingle to the thickest which are limited lifetime shingles, the cost
depending on the thickness and durability of the shingle. When a layer of shingles wears out, they are usually stripped, along
with the underlay and roofing nails, allowing a new layer to be installed. An alternative method is to install another layer
directly over the worn layer. While this method is faster, it does not allow the roof sheathing to be inspected and water
damage, often associated with worn shingles, to be repaired. Having multiple layers of old shingles under a new layer causes
roofing nails to be located further from the sheathing, weakening their hold. The greatest concern with this method is that
the weight of the extra material could exceed the dead load capacity of the roof structure and cause collapse. Because of
this, jurisdictions which use the International Building Code prohibit the installation of new roofing on top of an existing roof that has two or more applications of
any type of roof covering; the existing roofing material must be removed before installing a new roof.[5] Slate is an ideal, and durable material, while in the Swiss Alps roofs are made from huge slabs of stone, several inches thick. The slate roof is often considered the best
type of roofing. A slate roof may last 75 to 150 years, and even longer. However, slate roofs are often expensive to install
– in the USA, for example, a slate roof may have the same cost as the rest of the house. Often, the first part of a
slate roof to fail is the fixing nails; they corrode, allowing the slates to slip. In the UK, this condition is known as "nail
sickness". Because of this problem, fixing nails made of stainless steel or copper are recommended, and even these must be protected from the weather.[6] Asbestos, usually in bonded corrugated panels, has been used widely in the 20th century as an inexpensive, non-flammable roofing material
with excellent insulating properties. Health and legal issues involved in the mining and handling of asbestos products means that it is no longer used as a new roofing
material. However, many asbestos roofs continue to exist, particularly in South America and Asia. Roofs made of cut turf (modern ones known as green roofs, traditional ones as sod roofs) have good insulating properties and are increasingly encouraged as a way of "greening" the Earth. Adobe roofs
are roofs of clay, mixed with binding material such as straw or animal hair, and plastered on lathes to form a flat or gently
sloped roof, usually in areas of low rainfall. In areas where clay is
plentiful, roofs of baked tiles have been the major form of roofing. The casting and firing of roof tiles is an industry that is often
associated with brickworks. While the shape and colour of tiles was once regionally distinctive, now tiles of many shapes and colours are produced commercially,
to suit the taste and pocketbook of the purchaser. Sheet metal in the form of copper and lead has also been used for many hundreds of years. Both are expensive but durable, the vast copper roof of Chartres Cathedral, oxidised to a pale green colour, having been in place for hundreds of years. Lead, which is sometimes used for church roofs,
was most commonly used as flashing in valleys and around chimneys on domestic roofs, particularly those of slate. Copper was used for the
same purpose. In the 19th century, iron, electroplated with zinc to improve its resistance to rust, became a light-weight, easily transported, waterproofing material. Its
low cost and easy application made it the most accessible commercial roofing, worldwide. Since then, many types of metal roofing have been developed. Steel shingle or standing-seam roofs last about 50 years or more depending on both
the method of installation and the moisture barrier (underlayment) used and are between the cost of shingle roofs and slate
roofs. In the 20th century a large number of roofing materials were developed, including roofs based on bitumen (already used
in previous centuries), on rubber and on a range of synthetics such as thermoplastic and on fibreglass. - Outer layer
Thatch, using rice straw, Japan repairing thatch, Gassho-zukuri farmhouse, Japan
FunctionsInsulationBecause the purpose
of a roof is to protect people and their possessions from climatic elements, the insulating properties of a roof are a consideration
in its structure and the choice of roofing material. Some roofing materials,
particularly those of natural fibrous material, such as thatch, have excellent insulating properties. For those that do not,
extra insulation is often installed under the outer layer. In developed countries, the majority of dwellings have a ceiling installed under the structural members of the roof. The purpose of a ceiling is to insulate against heat
and cold, noise, dirt and often from the droppings and lice of birds who frequently choose roofs as nesting places. Concrete tiles can be used as insulation. When installed leaving a space between
the tiles and the roof surface, it can reduce heating caused by the sun. Forms
of insulation are felt or plastic sheeting, sometimes with a reflective surface, installed directly below the tiles or other
material; synthetic foam batting laid above the ceiling and recycled paper products and other such materials that can be inserted
or sprayed into roof cavities. So called Cool roofs are becoming increasingly popular, and in some cases are mandated by local codes. Cool roofs are defined
as roofs with both high reflectivity and high thermal emittance. Poorly insulated and ventilated roofing can suffer from problems such
as the formation of ice dams around the overhanging eaves in cold weather, causing water from melted snow on upper parts of the roof
to penetrate the roofing material. Ice dams occur when heat escapes through the uppermost part of the roof, and the snow at
those points melts, refreezing as it drips along the shingles, and collecting in the form of ice at the lower points. This
can result in structural damage from stress, including the destruction of gutter and drainage systems. DrainageThe primary job of most roofs is
to keep out water. The large area of a roof repels a lot of water, which must be directed in some suitable way, so that it
does not cause damage or inconvenience. Flat roof of adobe dwellings
generally have a very slight slope. In a Middle Eastern country, where the roof may be used for recreation, it is often walled,
and drainage holes must be provided to stop water from pooling and seeping through the porous roofing material. Similar problems, although on a very much larger scale, confront the builders of modern commercial
properties which often have flat roofs. Because of the very large nature of such roofs, it is essential that the outer skin
be of a highly impermeable material. Most industrial and commercial structures have conventional roofs of low pitch. In general, the pitch of the roof is proportional to the amount of precipitation.
Houses in areas of low rainfall frequently have roofs of low pitch while those in areas of high rainfall and snow, have steep
roofs. The longhouses of Papua New Guinea, for example, being roof-dominated architecture, the high roofs sweeping almost to the ground. The high steeply-pitched roofs
of Germany and Holland are typical in regions of snowfall. In parts of North America such as Buffalo, USA or Montreal, Canada, there is a required minimum slope of 6 inches in 12 inches, a pitch of 30 degrees. There are regional building styles which contradict this trend, the stone roofs of the Alpine
chalets being usually of gentler incline. These buildings tend to accumulate a large amount of snow on them, which is seen
as a factor in their insulation. The pitch of the roof is in part determined by the roofing material available, a pitch of
3/12 or greater slope generally being covered with asphalt shingles, wood shake, corrugated steel, slate or tile. The water repelled by the roof during a rainstorm is potentially damaging to the building
that the roof protects. If it runs down the walls, it may seep into the mortar or through panels. If it lies around the foundations
it may cause seepage to the interior, rising damp or dry rot. For this reason most buildings have a system in place to protect the walls of a building from most of the roof water. Overhanging eaves are commonly employed for this purpose. Most modern roofs and many old ones have systems of valleys, gutters,
waterspouts, waterheads and drainpipes to remove the water from the vicinity of the building. In many parts of the world, roofwater is collected
and stored for domestic use. Areas prone to heavy snow benefit from
a metal roof because their smooth surfaces shed the weight of snow more easily and resist the force of wind better than a
wood shingle or a concrete tile roof. - Insulation,
drainage and solar roofing
The flat roofs of the Middle East, Israel The overhanging eaves of China
Solar roofsNewer systems include solar shingles which generate electricity as well as cover the roof. There are also solar systems available that generate hot water or hot air and
which can also act as a roof covering. More complex systems may carry out all of these functions: generate electricity, recover
thermal energy, and also act as a roof covering. Solar systems can be
integrated with roofs by: - integration
in the covering of pitched roofs, e.g. solar shingles.
- mounting on an existing roof, e.g. solar panel on a tile roof.
- integration in a flat roof membrane using heat welding, e.g.
PVC.
- mounting on a flat roof with a construction and additional weight to prevent uplift
from wind.
Gallery of roof shapes- Roof shapes
Pitched roof with decorated gable, Chang
Mai, Thailand Sateri roof (with vertical break in pitch),
Sweden Flat roofs, Haikou City, Hainan, China Graded roof with a spared spot used as
a roof garden, Münster
Gallery of significant
roofsRoof components History References | Wikimedia
Commons has media related to Roofs. |
|